Process for Making a New Neckpiece
- by Linda Kaye-Moses
- Dec 26, 2016
- 19 min read
All Photography by Artist (using cell phone)
None of the following material, text and images, may be used without the written permission of Linda Kaye-Moses
To Begin,
I’ll just ramble through my process. All the images will have been shot using my cell phone and may not be high quality, but I think you will be able to see the process at any rate, and that’s all that matters. I’m a complete klutz when uploading images to fb, so you may find separate posting for related images. Sorry ‘bout that!
Any questions this group/individuals may have, just post them here, and I’ll try to answer them.
The piece began with a large oval Dendritic Agate (from Rare Earth Mining Company). The image of the dendrites referenced a tree in Winter, and reflected my feelings about the political situation in America, with the values of our country so severely compromised, appearing to have died (forgive me, if any of you reading this do not feel this way at all, or as keenly as do I). So the neckpiece would be about the reinvigoration of life. I had heard a quotation from Mexico (you may have read it here), “You tried to bury us. You forgot we were seeds” and I wanted the piece to be about that, with the intention of using that as the title of the piece.
Here’s a quick picture of the agate.
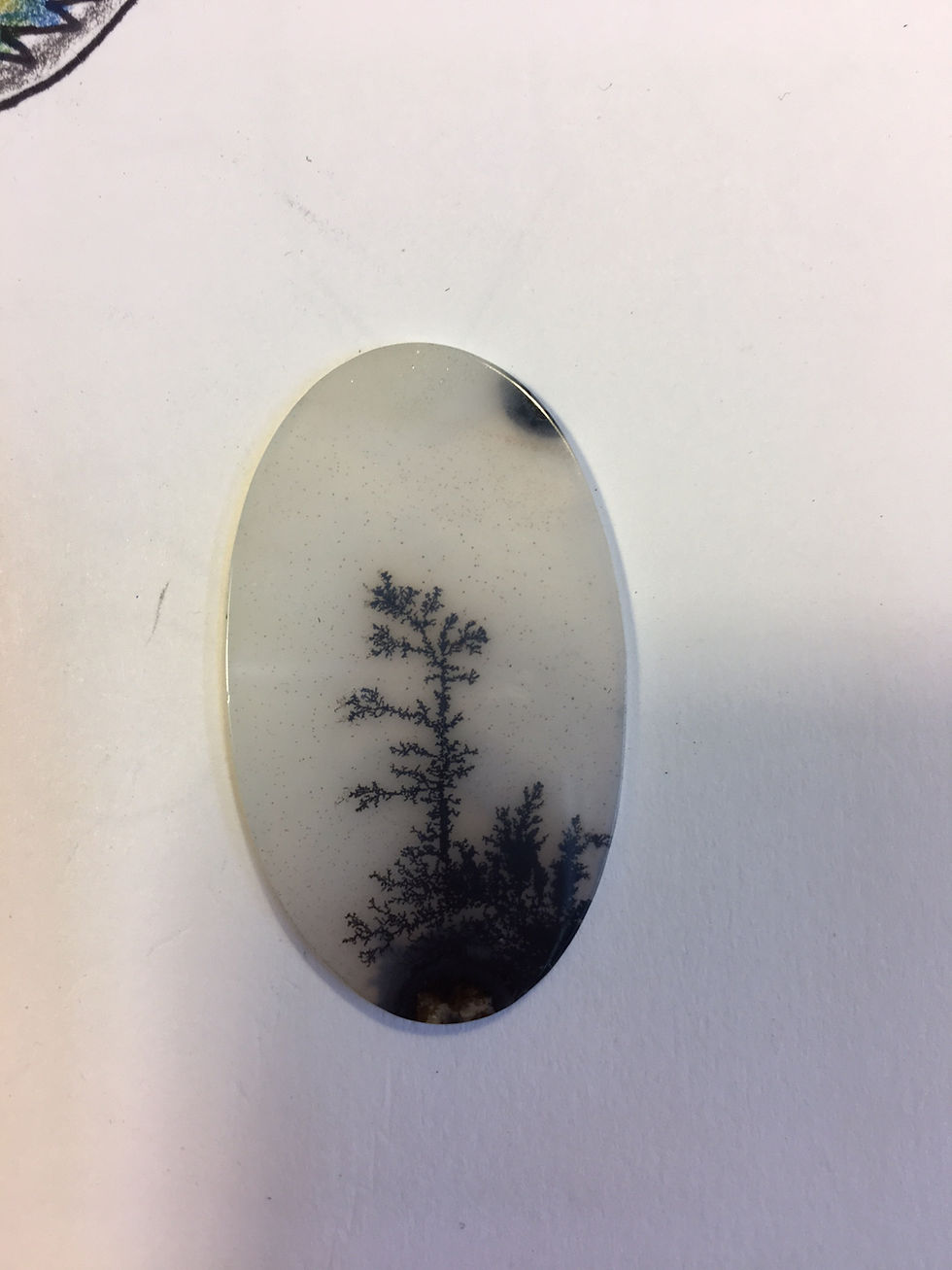
I began to draw a pendant, based around the agate. I wanted to include green leaves, bursting with life around the base of the agate, as if growing from below ground. So I would be enameling those leaves. I also wanted to have the piece ‘caress’ the body, just below and near the neck of the wearer, not simply attach a chain. That required that I include several extra leaves. There would also be a repeat of the leaves, set with a gemstone, for the clasp. The leaves would be enameled and/or granulated or both.
I use Prismacolor pencils to add color to my sketches, as this gives me a preview of what my pieces will look like with their stones in place. It’s sort of like getting Chanukah presents a little early.
Since I am a gemstone freak, I also wanted to include a range of stones, consistent with my jewelry design sense. The stones I chose were: a boulder opal, a lavender chalcedony, a citrine, and several small faceted amethysts (from a damaged bracelet that had belonged to my maternal grandmother who I had never met), and a carved aquamarine.

Here’s the drawing of the clasp.

The leaves would be made from fine silver metal clay (PMC3), supported by a backplate of sterling silver sheet. I decided to add a leaf on the reverse of the backplate, either soldered on or riveted. To be decided later. Many of my pieces, perhaps even all of them, evolve as they are being made, with decisions based on that evolution. This one would be no different.
I needed to create a printing plate to create the leaves. My preference is to use blockprinting plates which, when carved, create nice cells for enamels. (You can check out how to do this in my book “Fine Silver Metal Clay Beads”, since I don’t want to take up space here with all of that info). It’s a straightforward, hands-on process that has always worked for me, both with and without enamels: transfer the design to the plate; carve the plate; roll the metal clay onto the plate (final thickness, 3 cards); refine the clay. Because of the shrinkage of metal clay, I needed to enlarge the drawings 116%, which is the increased size that has worked for me. I use a photocopier with toner, because I can use the toner copy to transfer the image to the printing block. Here are the images from the copier and the printing plates.


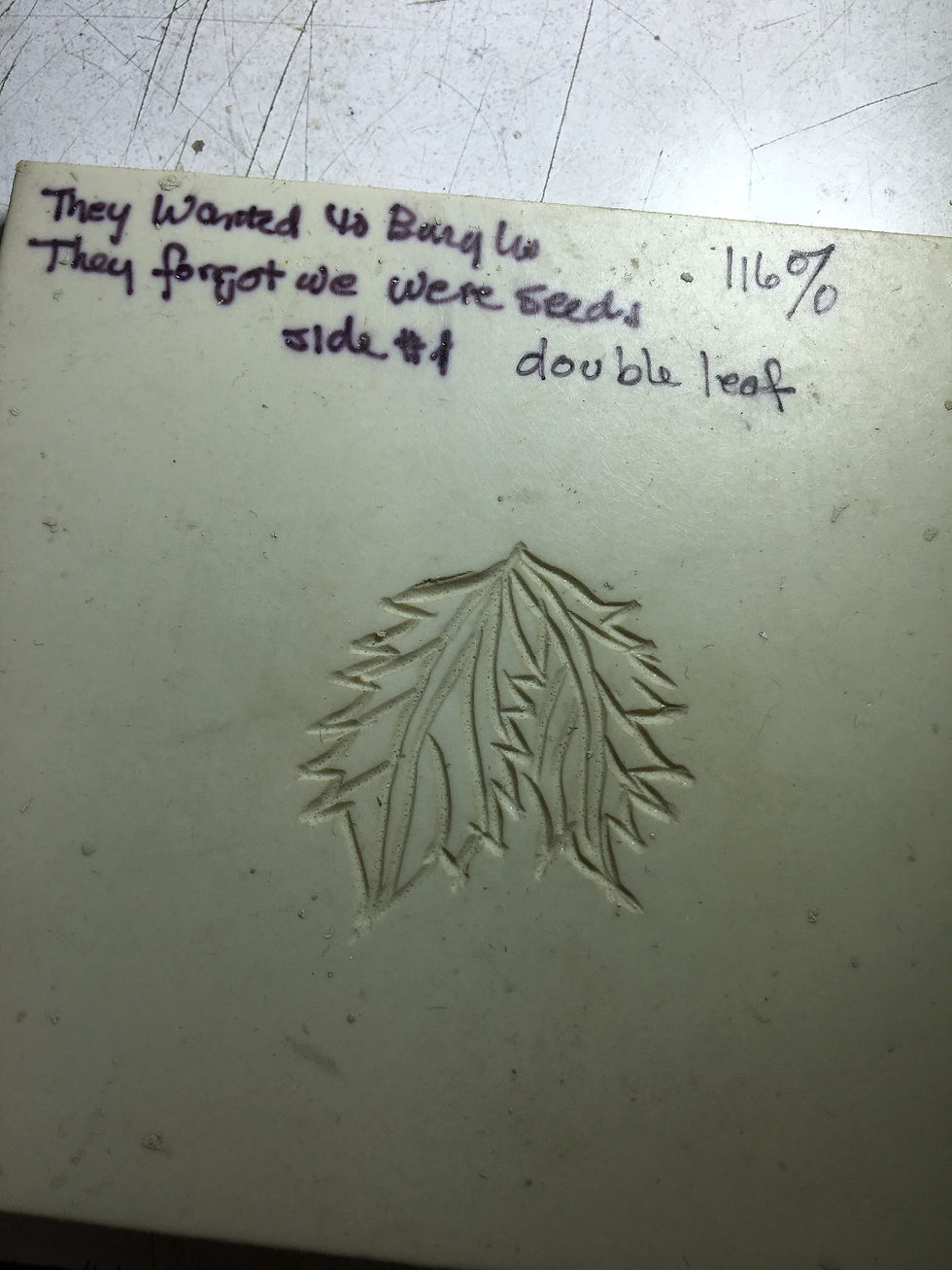

I next rolled all the leaf elements onto their respective printing plates.




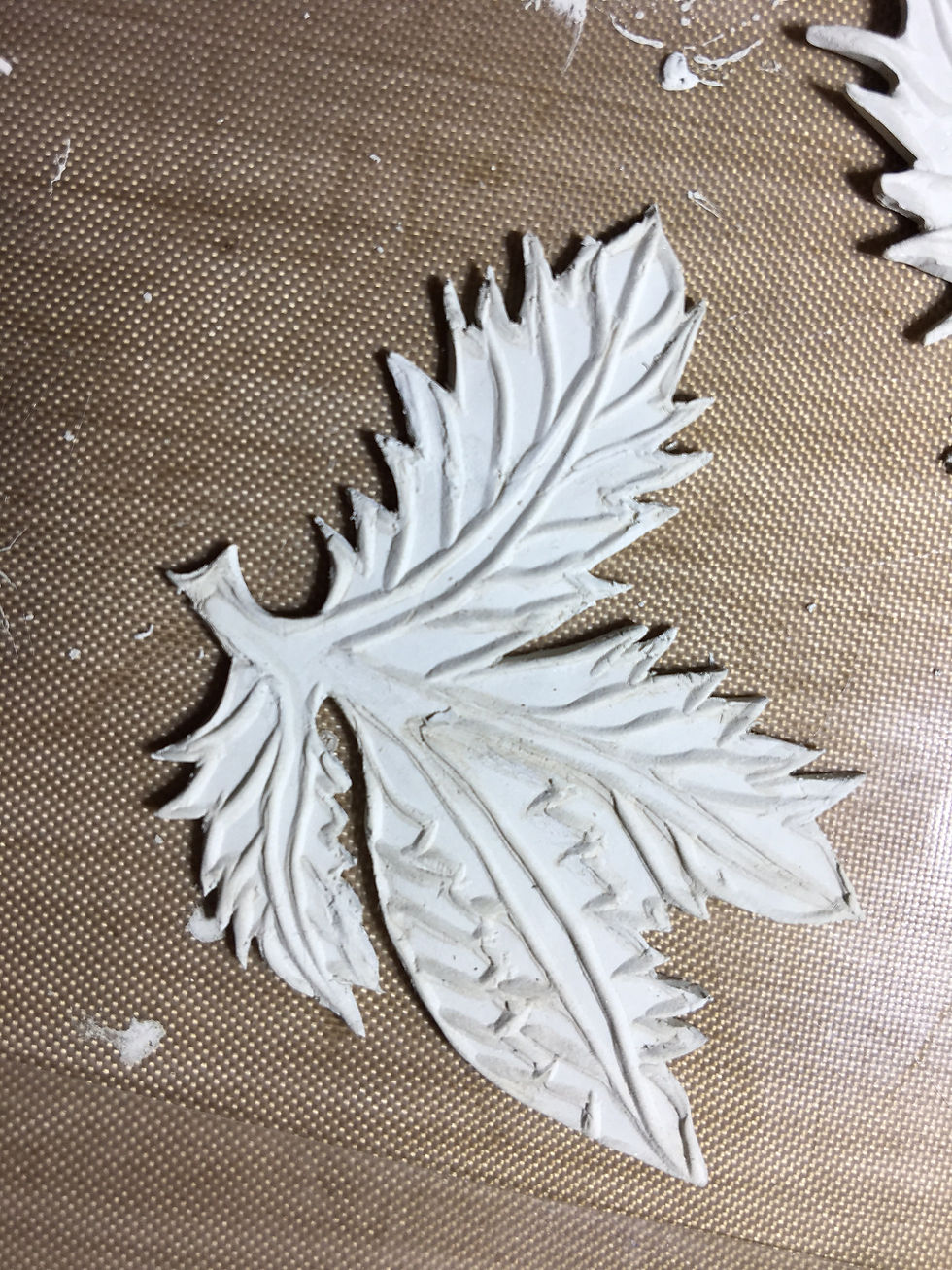
The leaves were to be quite a bit smaller than some of the work I’ve done in the past, and presented quite a challenge trimming the clay, with many of the points on the leaves deciding to snap off as I refined them. Repair, repair, repair.
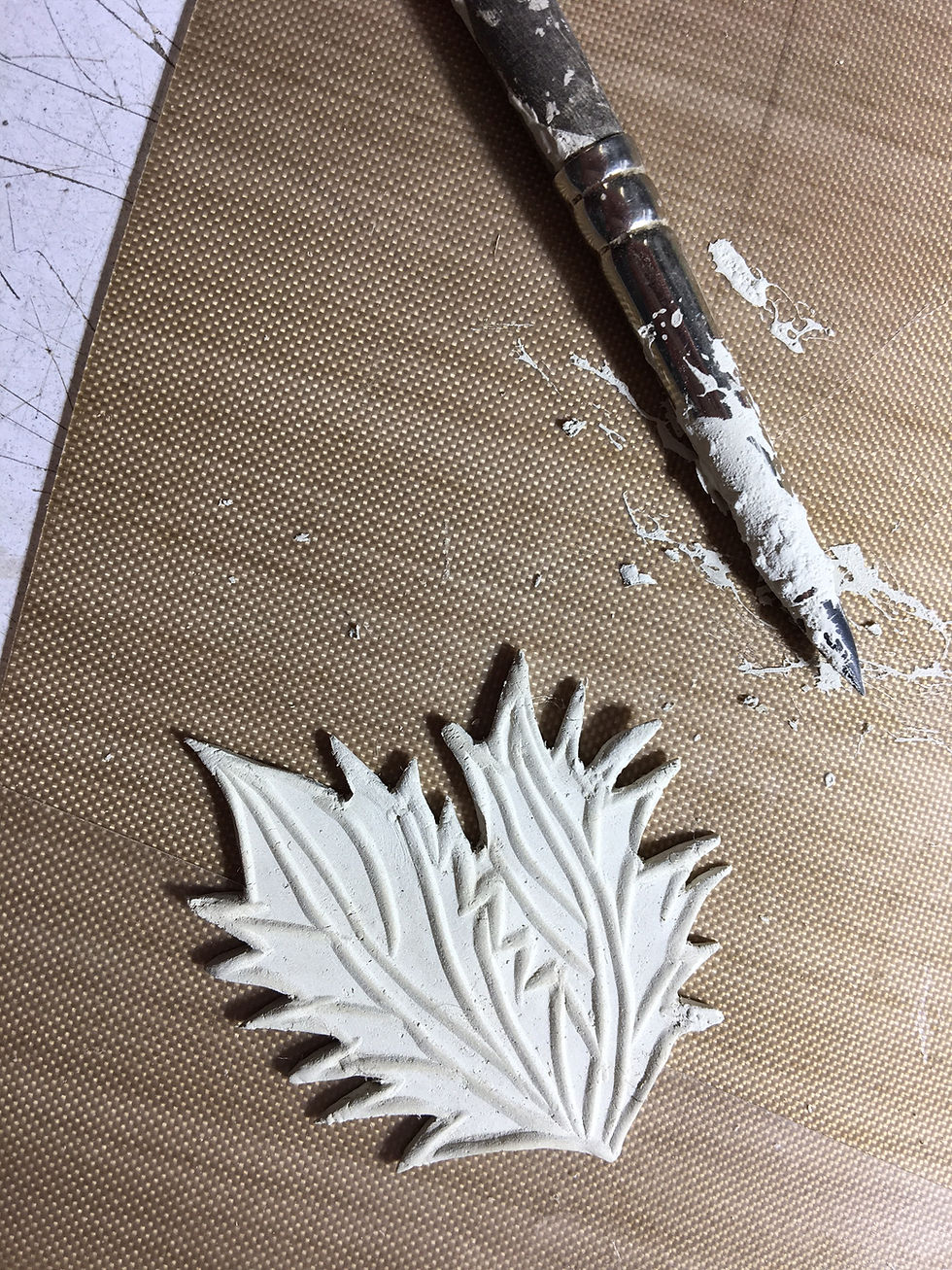
Once the leaves were completed, I needed to make several other mc elements: the stone support for the clasp and the bails for the central pendant. The stone support was a simple, 5-card thick disc... easypeasy. The bails were two short lengths of extruded square tubes. Once the disc and two small leaves were dry, I joined them together (see image) using Slip (paste) and dried them. After the clasp was dry, it was refined and smoothed.

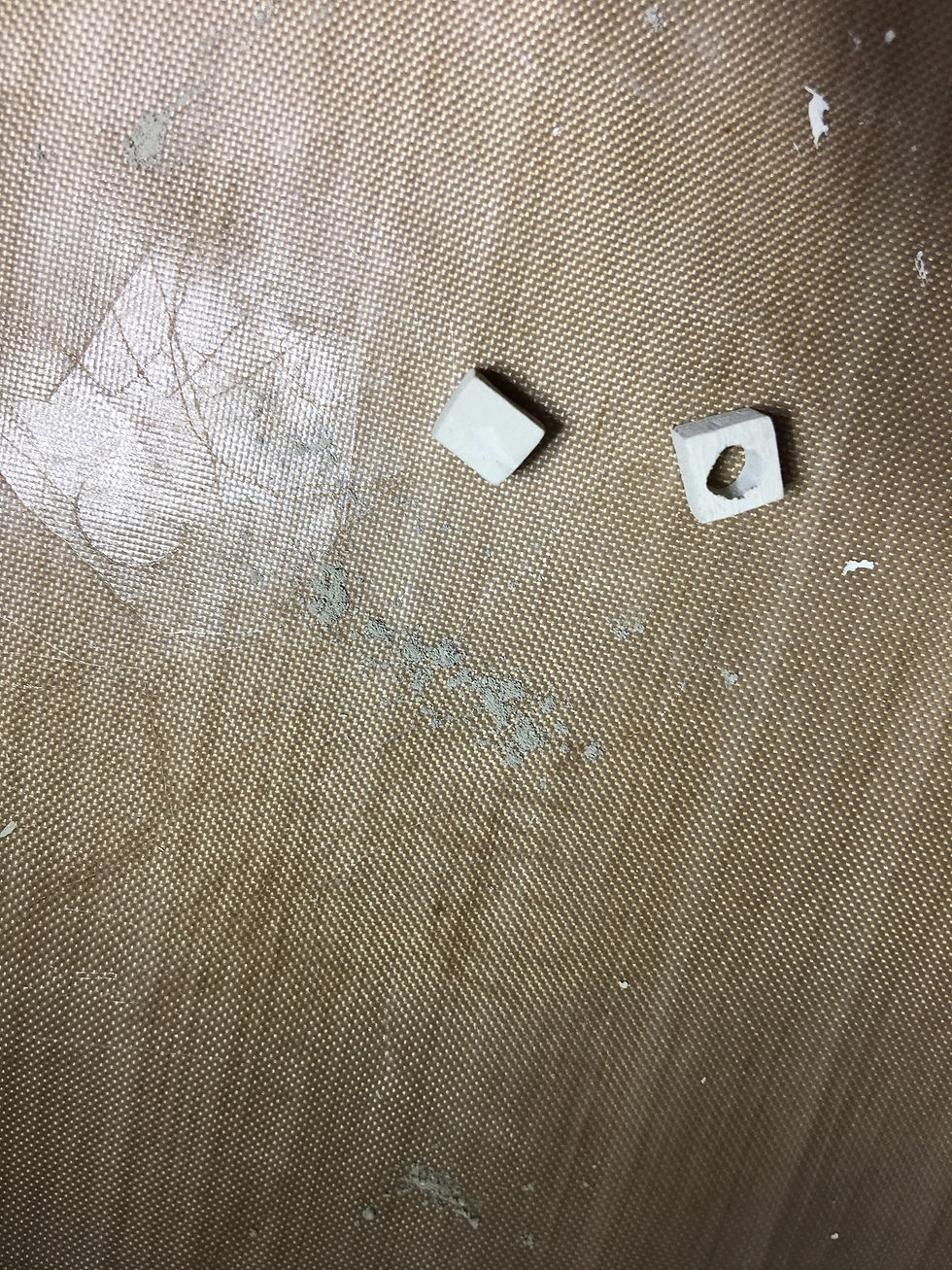
Once the bails were dry, I granulated them. (see image). The granules are equally sized spheres of fine silver. My process is as follows: moisten the area to be granulated; apply a generous amount of Slip (paste) to that area; place the piece to be granulated in a small container; sprinkle the granules onto the piece, gently shaking the container; carefully lift the piece out of the container, allowing excess granules to fall back into the container; place piece on a flat surface and use a flat tool (I use the back end of a pair of soldering tweezers) to press the granules down gently; dry.
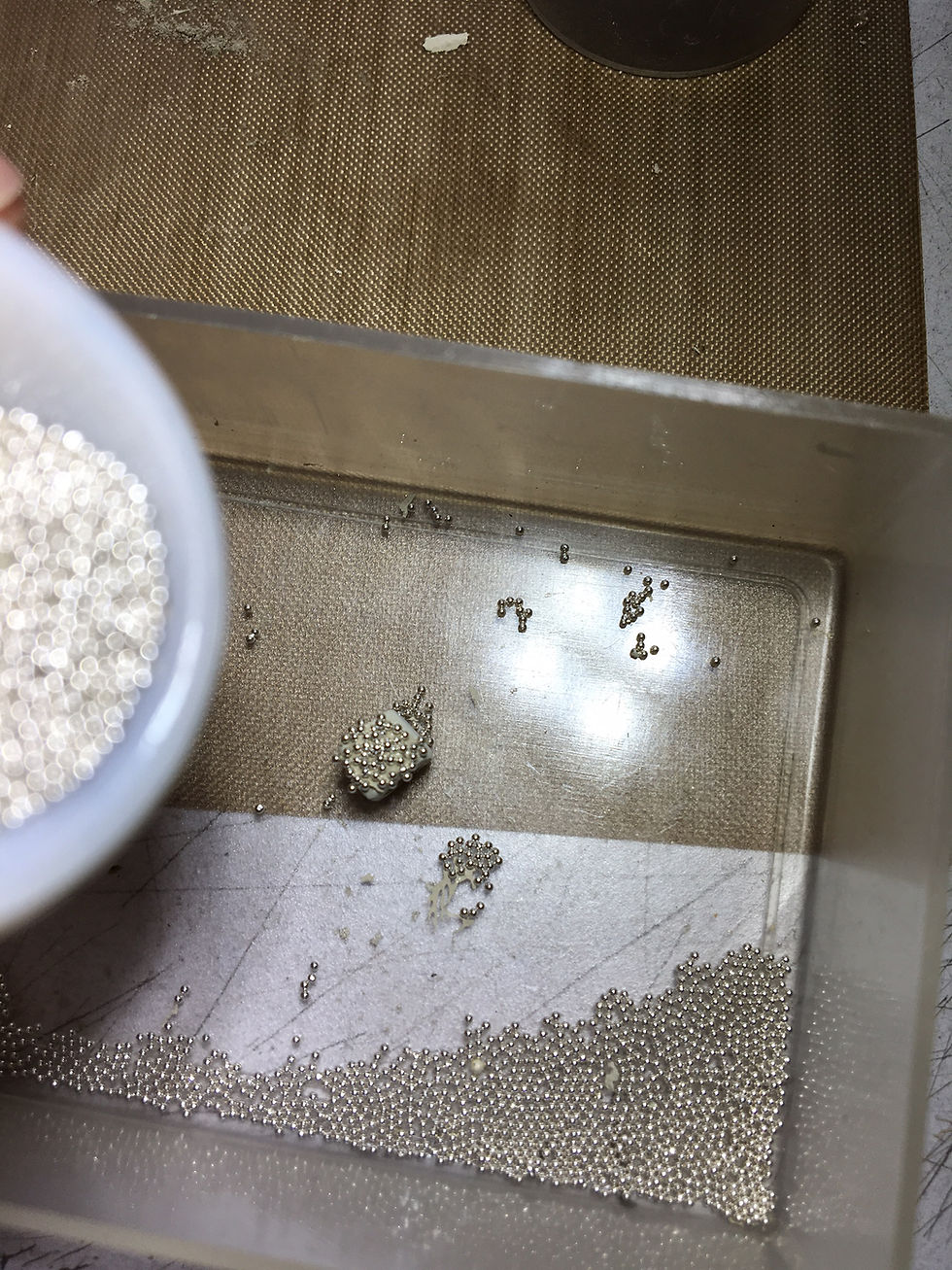
The bails will be soldered to the sterling silver backplate after the bails have been fired and the backplate has been fabricated.
After the leaf elements have dried, I selectively granulated them as well.

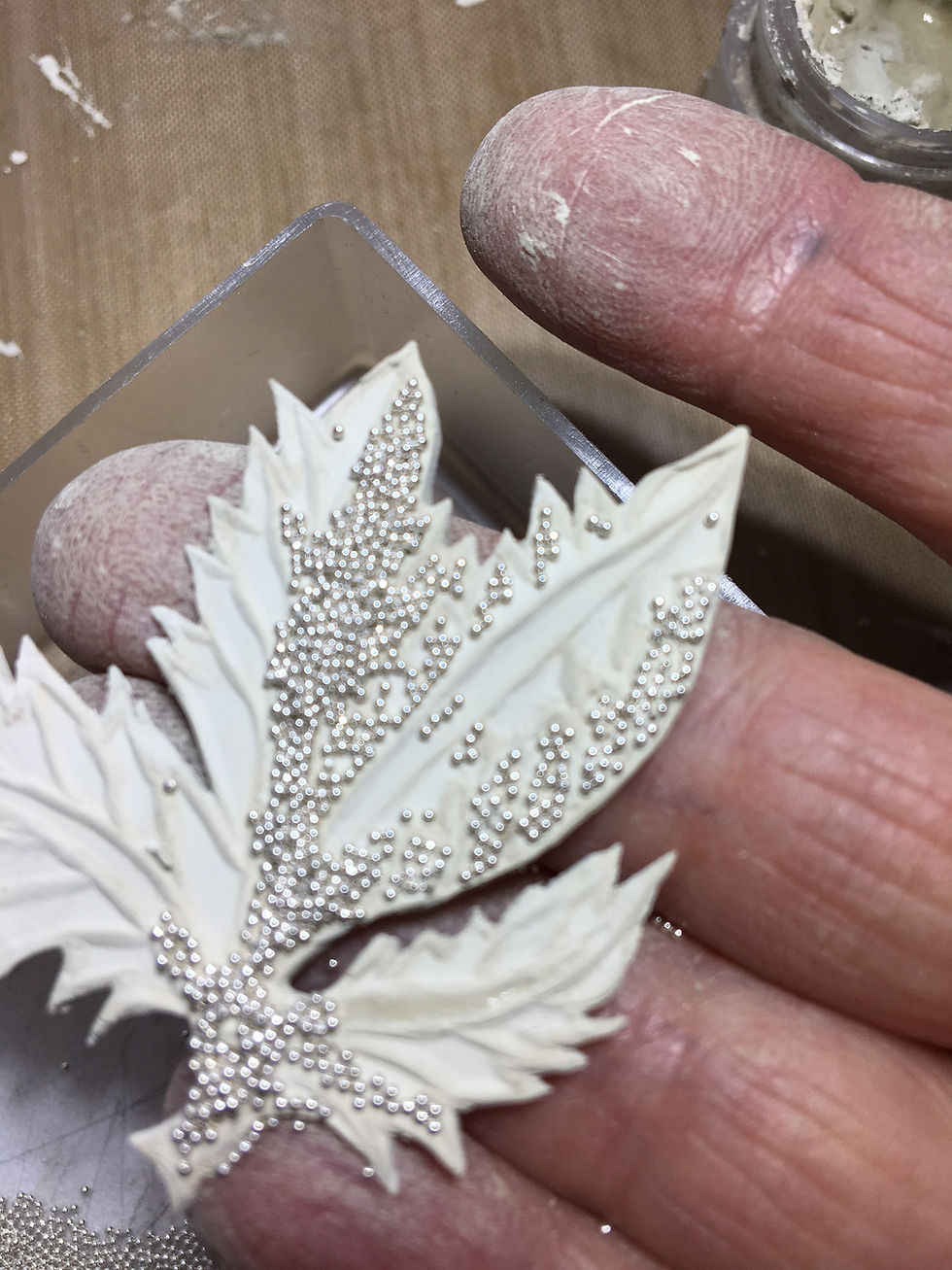


One thing I wanted to have happen is a slight curving of the elements, including the clasp. Because the granules do not shrink, and the body of the mc clay elements will shrink during the firing, that shrinkage should cause the parts to curve. We’ll see.
Once all the pieces are dry the final refining process is done, including replacing granules that may have fallen off, and smoothing all the edges.
Next the pieces were placed on a thin layer of Alumina Hydrate on a kiln pad. I know that the pieces will shrink and curve a little, and I want them to be able to slide easily on the surface of the kiln pad, without cracking. The AH allows them to slide.

While the metal clay elements are firing, I just want to back up a little bit here. I think I am what one would call an intuitive maker, that is, I am moved by ideas, spirit, dreams, and heart. So, when I begin to make a piece, I bring all the design concepts together with those intangibles, and my materials and tools. The drawings that I do for each piece are frequently just the starting point, and, as a piece is being made, it may evolve, change direction, become something slightly (or hugely) different. This can be determined by screw-ups (by me), or changes in the way I’m thinking about how a piece will be fabricated and sometimes, what the materials begin to ‘say’ to me. For example, switched out the citrine for a faceted green quartz, which ‘felt’ right for the design. Don’t even try to ask me what ‘right’ is...it just is.
This long ramble about the latest neckpiece is showing you my path through fabrication of the neckpiece, and right now, today, I don’t know if the final piece will be identical to, similar to, or wildly different from my original vision for it. There are those artists who are capable of building their work so that the final manifestation of it is identical to their original concept for it. I’m not one of those, never have been, never will or can be. Just so ya know.
January 15, 2017
As I had hoped, the granulation forced the clay to curve as it sintered, producing a slight doming effect. I like this curvature and won’t adjust it further (See below for image).
The next step is to sand the back sides/edges of the center and side units so that they will sit neatly on their respective backplates. The intention is to set these units using 18k gold prongs.
It’s also necessary to soften the tips of each leaf so that they don’t act as weapons when the piece is being worn, scratching the skin or catching onto garments. Need to do this to the leaves on the clasp as well. I could have done a little of this before firing the leaf units, but they were too thin and fragile as unsintered greenware. It was best to wait until the material was sintered (solid metal).

While doing the sanding, I’m thinking about how to join these three units. Actually, no matter what I’m doing in this process, a part of my mind is also chewing on what will come next, how I want the piece to look and how I will get there.
What needs to be considered: design, design, design; efficiency; keeping the side units from flipping up or over; keeping the joining jump rings (whatever) from being oversized (this is a tendency of mine... to overbuild, and I want to avoid it); keeping the weight down for comfort’s sake.
The granulated bails and the oval leaf unit also need to be sanded so that they can be soldered to the back of the sterling silver backplate.
The clasp back is smoothed and then textured using the flex shaft, hammer handpiece, and scribe (sharp pointy tool) tip. This is a pattern that will make the bare surfaces of the neckpiece consistent...it brings all the parts together. I’ll do more of this later on, as the piece comes together.
The sterling sheet for the backplates is rolled on a rough sandpaper to give it a texture that has the appearance of the hammer handpiece texture, but a little more subtle. This texture will be the back of each plate. All texturing is done before any enameling or soldering, although I will probably do more once everything is soldered.

Roll-printing causes the sterling sheet to curved. To remove the curve, I anneal the sheet. To anneal the sterling, I mark it with a squiggle (a technical term!!) using a fat permanent marker. When the sheet is heated to annealing temperature, the mark disappears, and I place a block of charcoal on top of the sheet to flatten it.

Ordinarily, to anneal sterling, I would heat it and then quench it in water. The quenching cools the metal swiftly and completes the annealing process. However, placing the charcoal on top of the heated sheet, accomplishes enough to allow me to flatten the sheet sufficiently.
Before beginning to enamel, the metal surface within each cell of the leaves is textured once again using the hammer handpiece,. Once the cells are enameled it will give those areas an extra ‘sparkle’. I can control the impact of the tip more easily with this tool, than simply using a hammer and a punch. Also, doing this manually would require that I place the units on a steel block, with the end result being a flattening of the form, which I want to avoid. Using the flex shaft, I can hold the units in my hand to achieve the overall texture I’m aiming for.

Before enameling the pendant units, I need to trace their perimeters, so that I can create the pattern for the backplates that will support them.
I create the pattern for the supporting backplates by simply drawing around the perimeters of the leaf units.
To transfer the pattern from my sketchbook to the sterling sheet, I stick removable clear tape to the drawing and trace the design, using a fine line black marker. I then remove the tape and press it on the untextured side of the sterling sheet. Following this pattern, I use a jeweler’s saw to saw it out, removing the tape when I’m done.
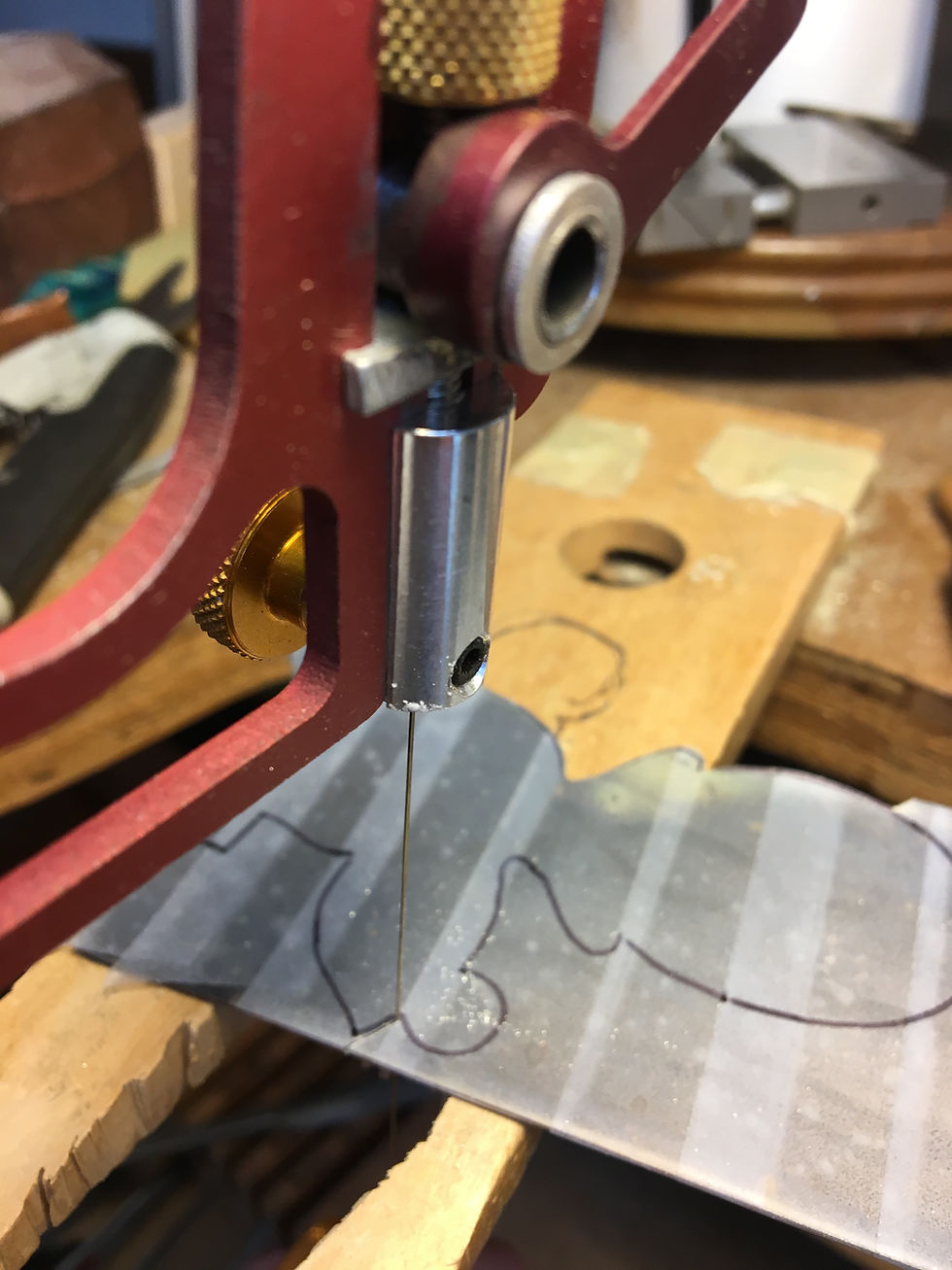
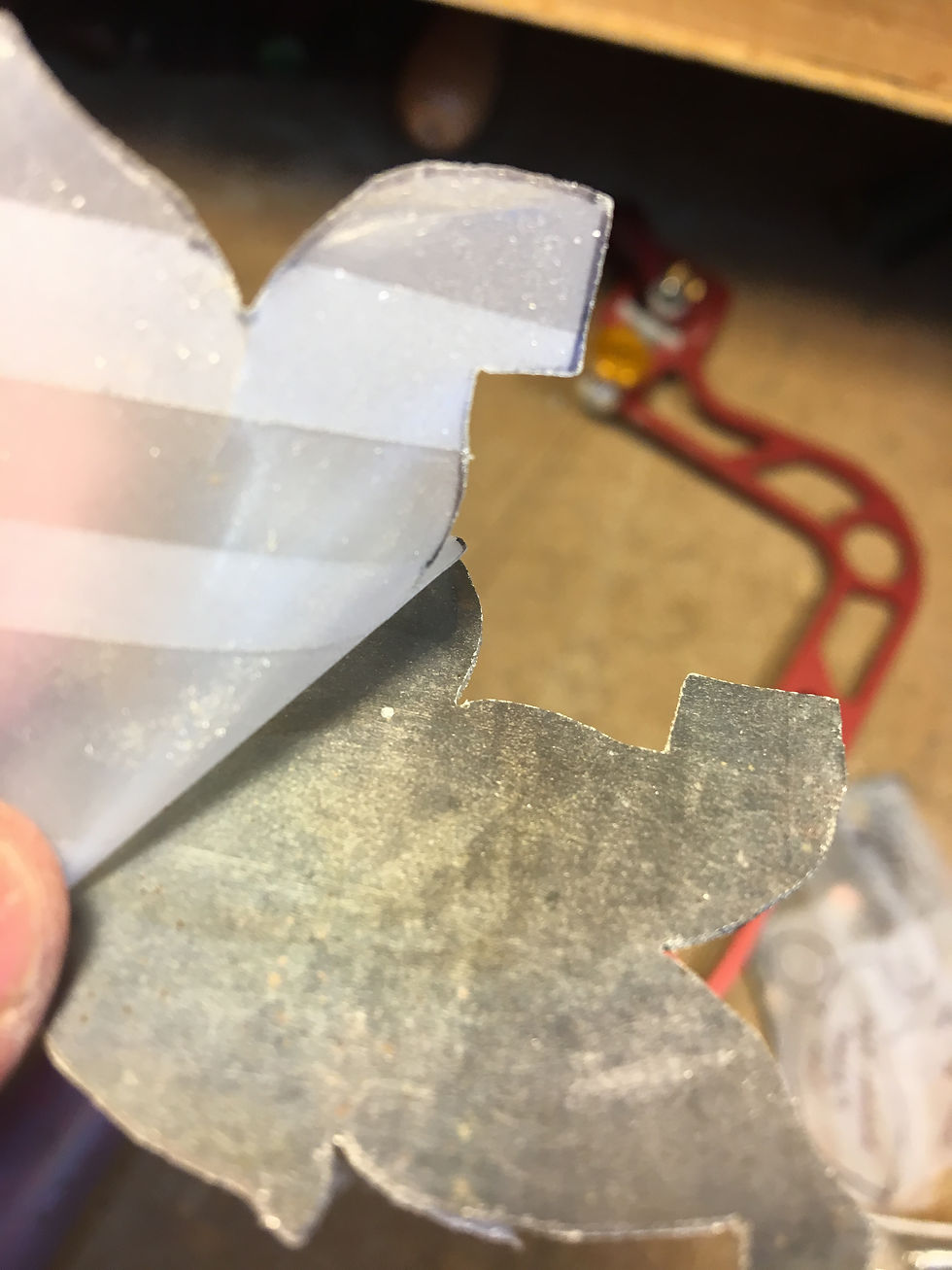
Here’s what the backplates will look like, leaving additional room for the prongs and a little ‘wiggle room’ for me to mess up, if that happens (‘when’ that happens).
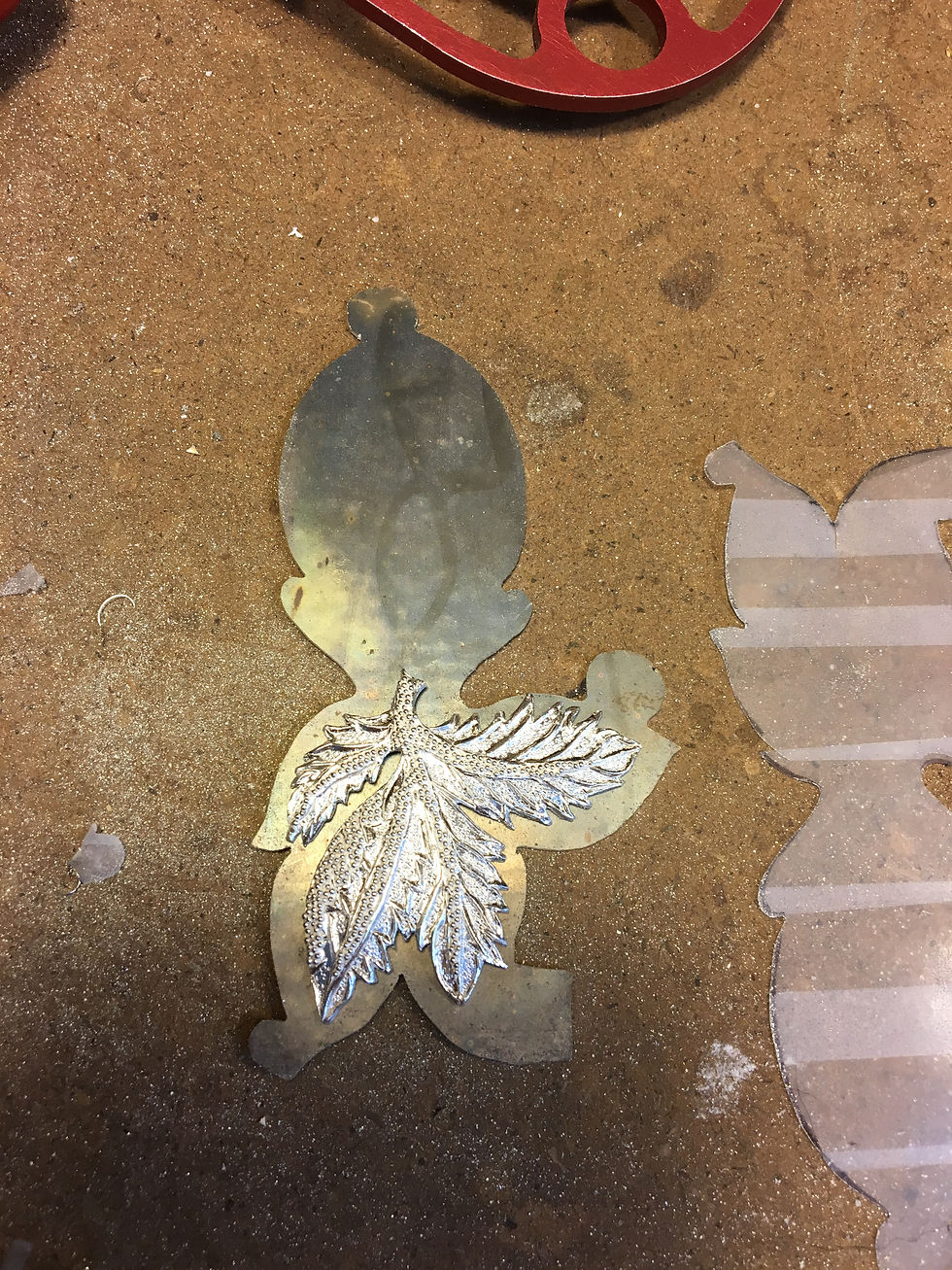
The small ‘buds’ extending from the edges are supports for small units of 18k yellow gold. The larger extensions will support the stones, and are checked against the size of the stones and adjusted accordingly. I do make the backplates a little larger than they might eventually need to be, just in case, for example, if the enameled units flatten a little in the kiln.
I want the edges of the backplates to be upset (thickened) and textured. I do this now, even though I might have to re-do it if I have to adjust the size and shape once the enamels are fired. I use the flex shaft again, with a small gear from an old alarm clock as the tool.

The back of the central backplate will have the oval leaf unit soldered to it, plus the bails, plus a long vine-like unit traveling from the leaf to the back of the boulder opal extension (that’s my intention). This will be both decorative and structural, since the backplate is relatively thin for its size, and may need the extra support to prevent distortion during stonesetting and being worn.
The gemstones are to be bezel set, using fine silver bezels. The perimeter of each stone is determined wrapping it with a strip of masking tape, trimmed to the exact perimeter (plus a small amount longer to allow for filing the ends).
The height for each bezel is determined using a steel divider, then the bezel strip is scribed with that tool, using the masking tape to measure the correct length.
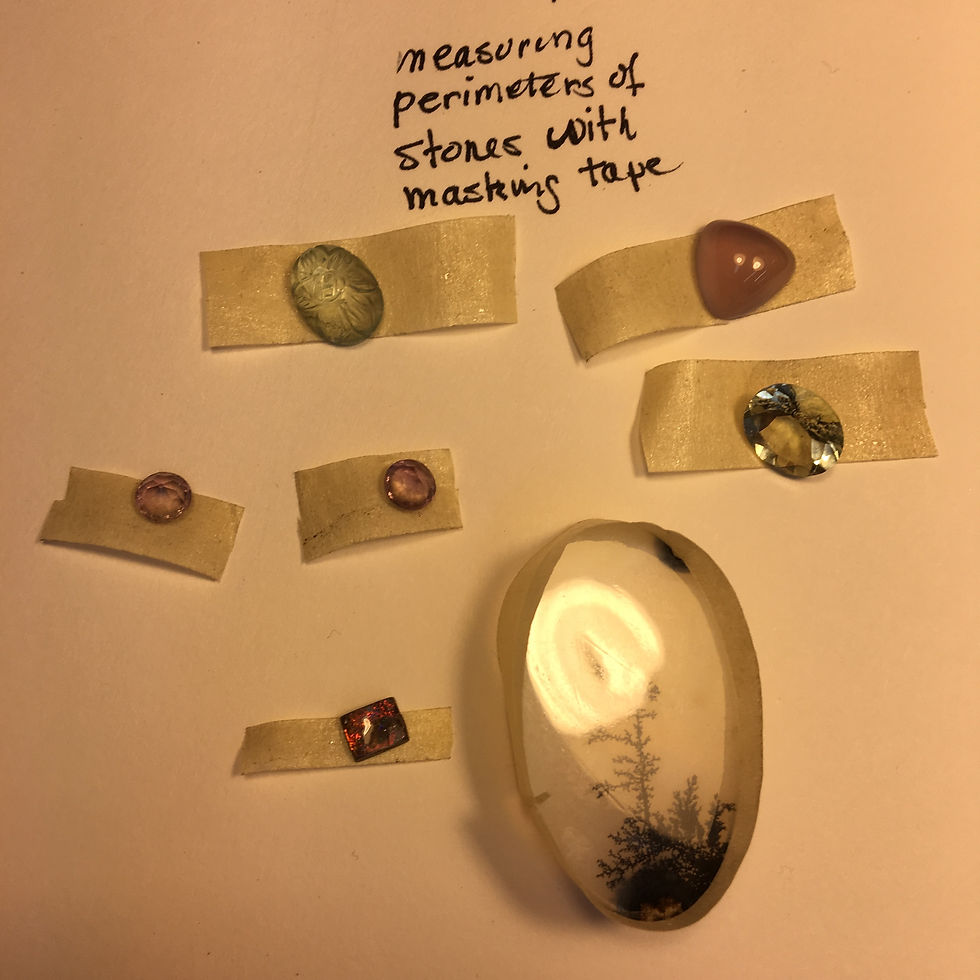
I cut the bezel, first at each end with a pair of flush cutters, and then the length with a pair of scissors. The bezel strips are then annealed, to make it easier to bend around each stone to make certain the length is correct. I then file the ends of the bezel strips using a mill bastard file and a mitre jig, in order to create a true flush seam for ease of soldering the joint.

The ends of the bezels were then soldered, checked for size and height, on the stones, and adjusted if needed, and the base of each bezel was sanded flat to provide a good surface for soldering.
I’m still thinking about whether I want to raise the smallest stones on pedestals. Mulling it over as an option. But since I want to wait until after the ‘leaves’ have been enameled, I don’t have to make a decision right now.
(OK, I do decide to raise the three small stones on pedestals, so I saw short lengths of sterling silver round tubing to support the stones , I will solder each bezel to a small backplate that is, in turn, soldered to the tubing, which in turn will be soldered to the main central pendant backplate.

Even though it appears that I'm going to sawing a slanted tube, this image was used only to show how I use a tubing jig to cut tubing. I really did cut a level kerf in the tubing (REALLY!).
ENAMELING
Now for enameling...I will be using transparent lead-bearing enamels, in greens, aquas, and blues to use for shading the greens for the leaves. I will wet-pack the enamels.

I mix a solution of 3 parts distilled water to 1 part KlyrFire (an adhesive) and apply a drop of this into each color of enamel that I am using. Using a fine watercolor brush I apply the enamels to the fine silver units, beginning with the central pendant unit.
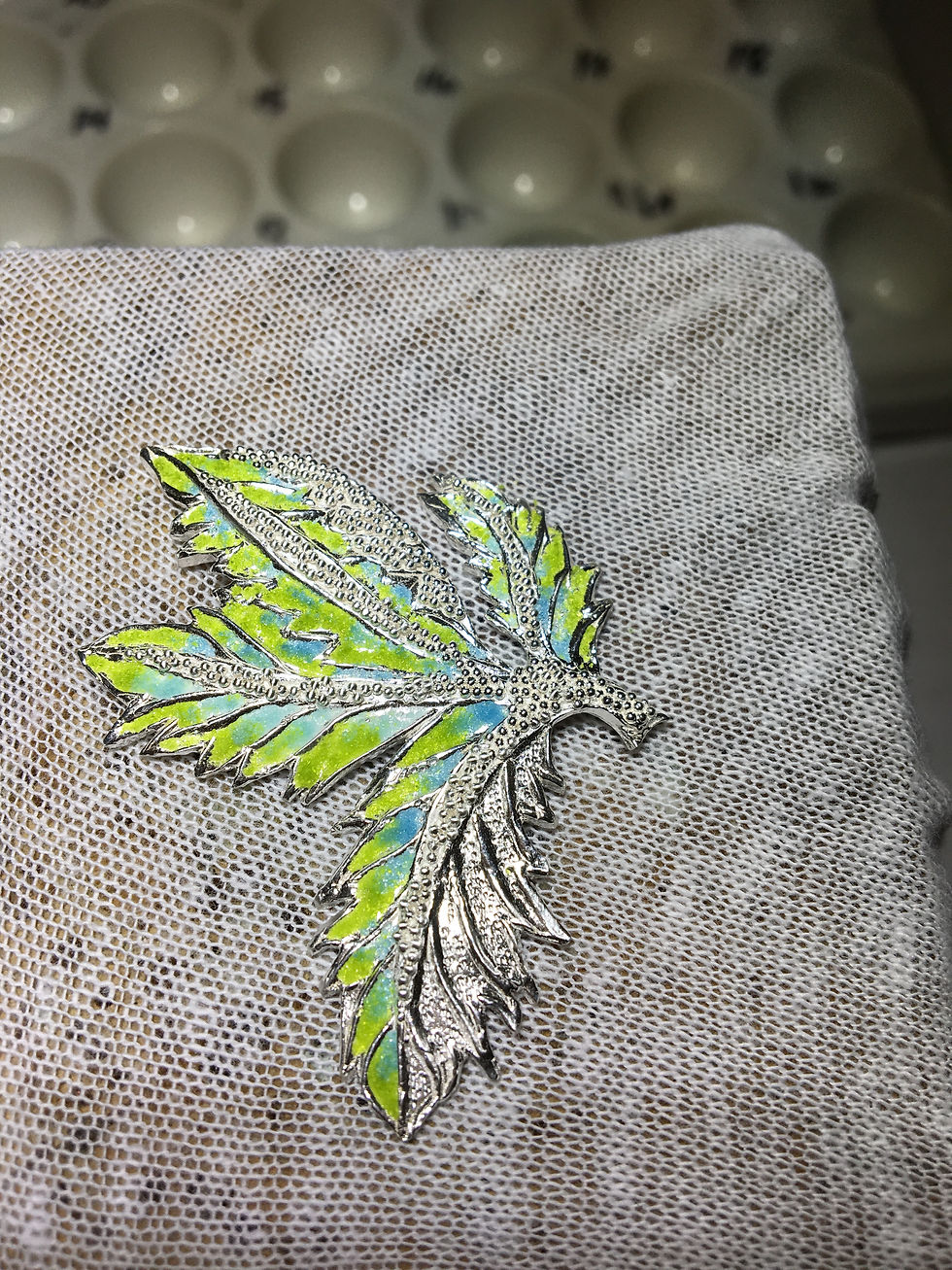
I need to consider that, while enameling the pendants, the curve may shift and change and there may be warping. I support them in the center while enameling them, in order to maintain the curve. I use a curved length of nichrome wire to support the enameled units.

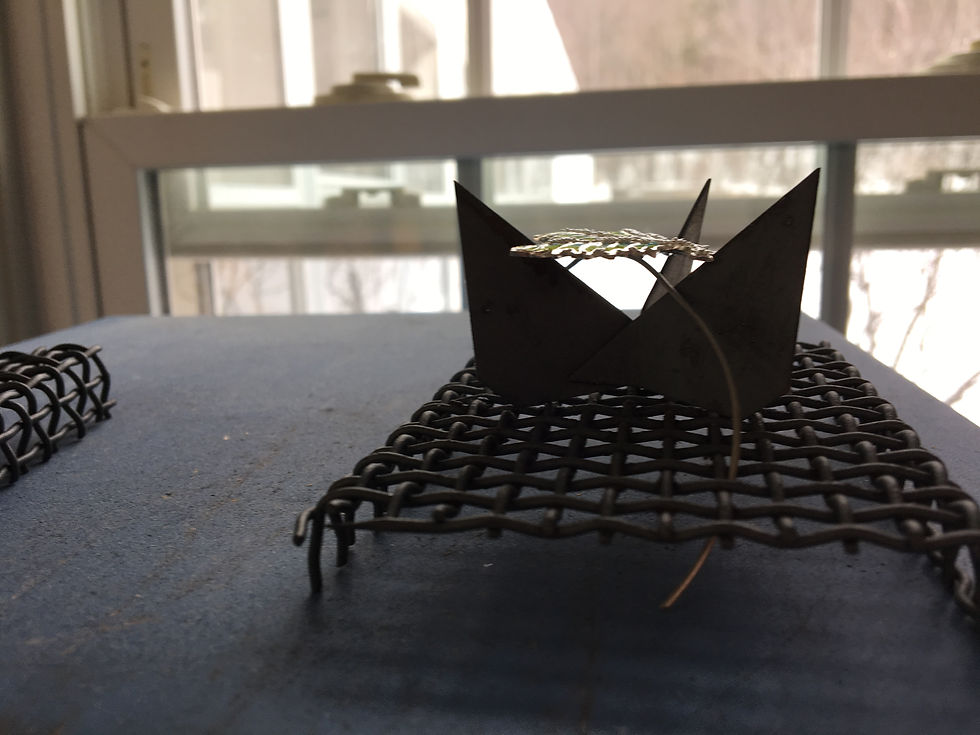
AFTER ENAMELING

Now I need to check to make sure that the sterling silver backplates are the right fit for the enameled units, and adjust them to fit properly. I check for the placement of the prongs and drill holes for them and a hole that will be behind the domed leaf unit.

I also drill small holes through the back of the bezels for the smallest stones, where the tubing pedestal supports will be soldered (to allow the solder to flow and heat to escape while soldering).
The CLASP
I make a sterling silver quality/logo plate. This is soldered to the underside of the clasp at the same time as a Sterling silver S-hook.

The bezel cup for the green quartz is fabricated and then soldered to front surface of the hook unit of the clasp.

I‘m thinking about the links that will join the central pendant to the side pendants, and the side pendants to the chain. I’ve made some links, large and small, using sterling silver balled/beaded wire wrapped with 24g sterling silver round wire. I’m liking the look of these... a little irregular, which suits my design sense… more to my liking than simple wire links. These will have to be joined to the chain with smaller jump rings.

I fabricate some cones from Sterling round wire that are to be used for the clasp loops.

The walls of these cones are soldered using Hard silver solder.
THE SAWING AND THE SOLDERING
I drill a hole in the backplate, where the domed leaf unit will be soldered (just behind where the bezel for the agate will be soldered. The hole is needed so that the domed unit will solder completely, without popping off due to the escaping heat. The hole will be hidden under the dome and behind the agate.
Beginning with the central pendant, I solder the bails, the domed leaf unit, and the vine to the back of the pendant.
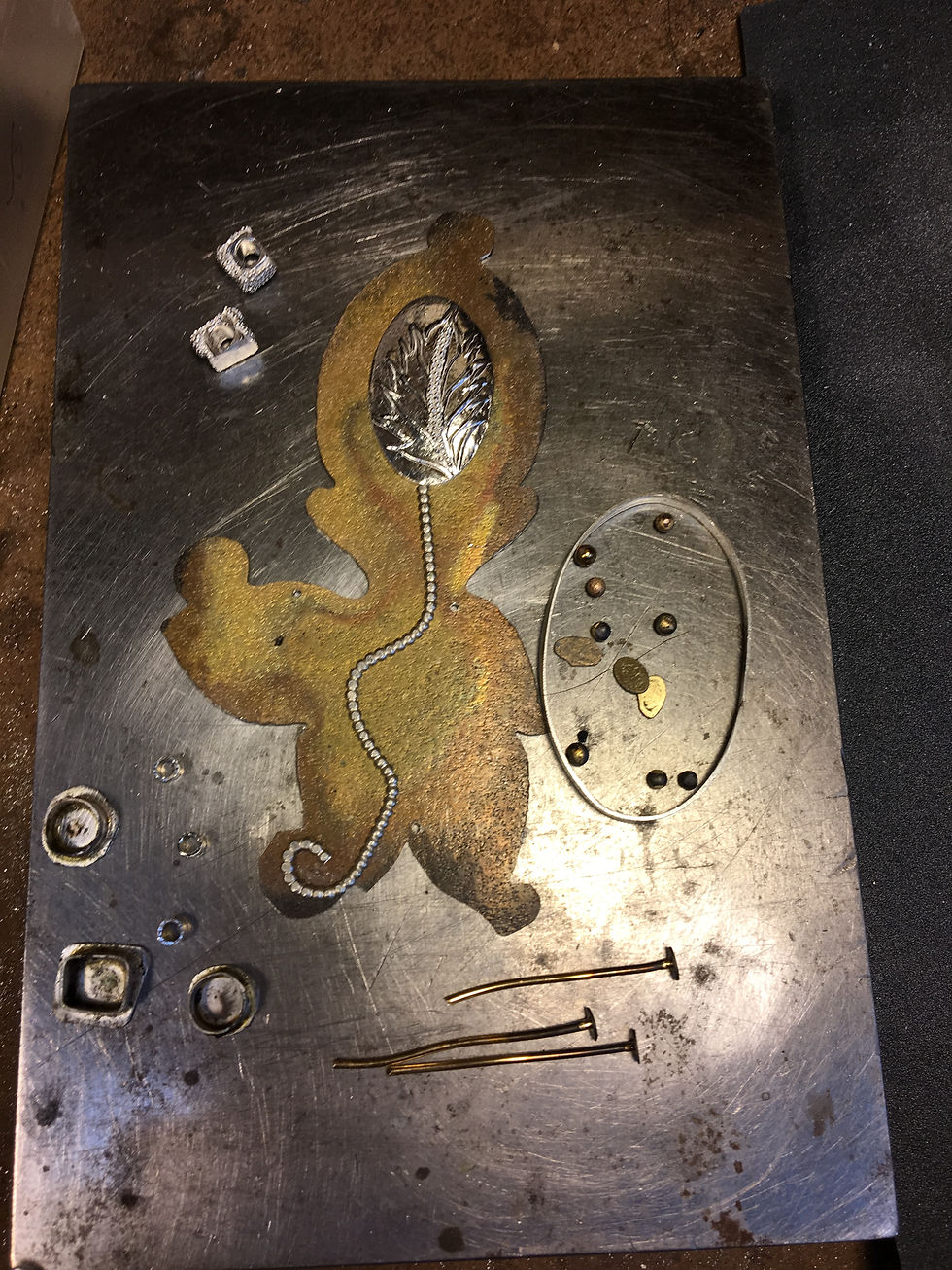
18k gold prongs will hold the enameled unit on the front. The tip of short lengths of this wire is beaded using a torch. The wire is then inserted in a fitting hole in a drawplate and the bead is tapped flat using a planishing hammer. This creates a flat head at one end of each of the wires. Each wire will then be slipped through a hole from the back of each backplate and soldered in place. These will not be soldered now as I want to use Easy solder and, therefore, they must be the last things soldered to this pendant.
I begin by soldering the Domed Leaf, Vine and Bails to the back of the central backplate. I use Hard Silver Solder.
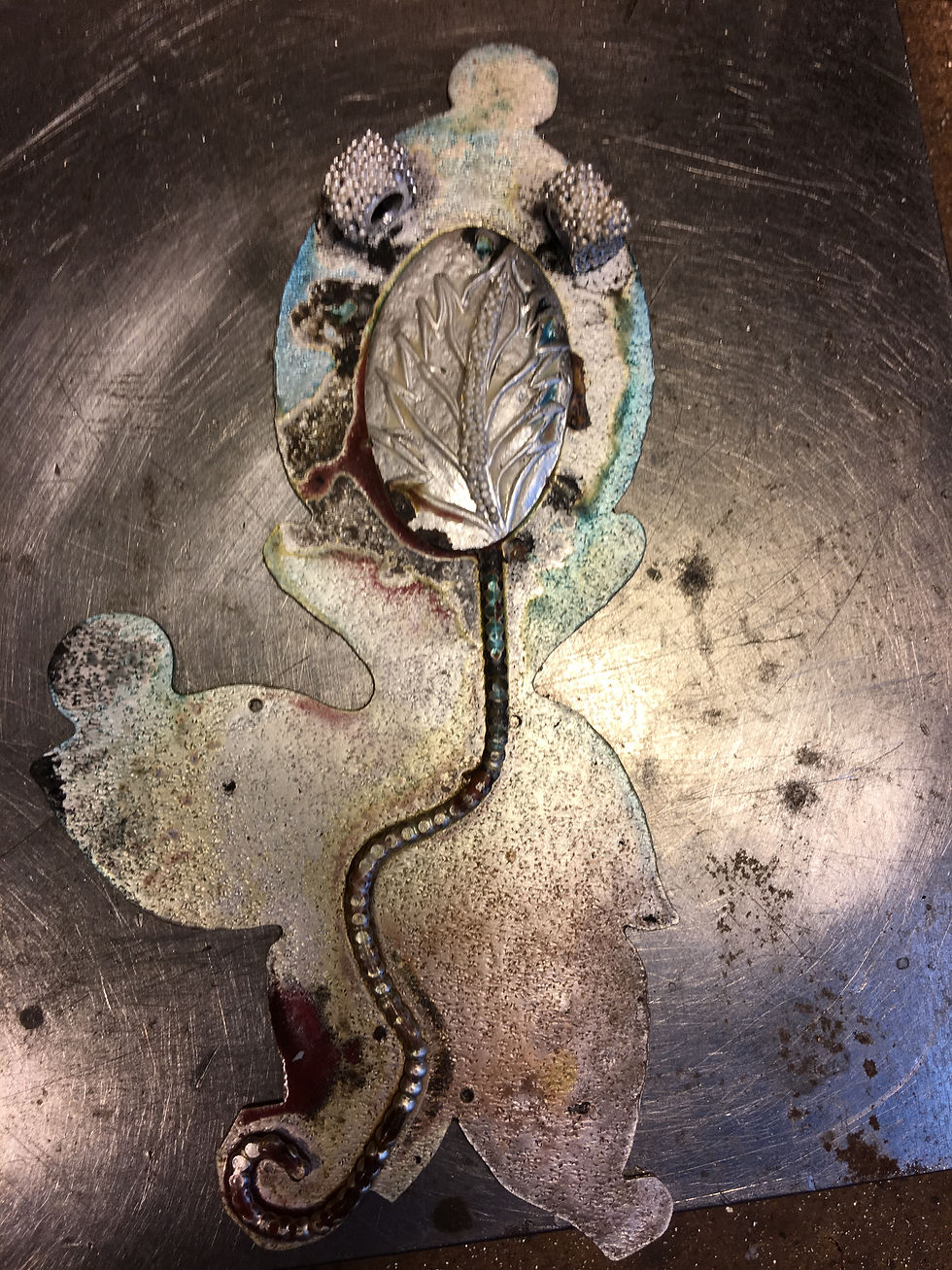
I paint the soldered areas on the back of the central pendant with a paste of Yellow Ochre/water to prevent the solder from re-flowing when I begin to solder everything on the front.
I place a large steel cotter pin on a soldering surface and place the central backplate on top of the cotter pin. This is such a large piece that I want the heat to circulate beneath it and over it. The cotter pin raises up the metal and allows this to happen.
I flux the entire front of the pendant. I flux and then melt a little Medium solder on the backs of three flattened ovoids of 18k gold, and then flux them again, and place them, and the small gem settings (on pedestals), the large agate bezel on the pendant, soldering them in place, using Medium Solder.

I need to solder several small granules of 18k gold to the side edges of the pendant, so I ochre the previous solder joints, front and back, and place the pendant right side up on a soft soldering block with depressions for the bails to rest in. This permits the edges of the pendant to rest on the surface, which will help to support the granules for soldering.
This feels like kind of a risky operation for me, as I’m concerned about overheating previously soldered joints and/or melting the large bezel, but all goes well and the granules are joined to the pendant satisfactorily.
Next step, I push the 18k gold prongs, from the back of the pendant to the front, through the holes I drilled previously, (extra long, because, if they are too short, you can’t make them longer again). The flat or nail head on the prongs are soldered from the back of the pendant, securing the prongs in place. The gold heads are intended to be decorative on the back of the pendant.
The moment of truth…checking the fit of the prongs for the enameled unit for the central pendant. Woooohoooo! Happiness!


Once the soldering operations are complete the piece is pickled for two reasons. There is so much flux and ochre that has been heated onto the piece that simply boiling the piece in baking soda would not remove it (normally my preferred process), and the pendant has been heated so many times, there would be considerable firescale that needs to be removed. Ordinarily, I don’t worry about firescale, because the shadows meld with the patination I always use, but this time, I really want to remove the excess firescale.
Next I boil the pendant in a saturated solution of baking soda, because I want all of the pickle to be neutralized. Since there are holes in the back of the small bezels to allow them to have been soldered to their hollow pedestals, pickle could have gotten inside the tubing. This has to be neutralized. Also, pickling sintered fine silver (from metal clay… the domed leaf unit), can result in the material absorbing pickle as well. This also needs to be neutralized. 20 minutes in the boiling baking soda solution should do the trick.
NOTE: Unneutralized pickle leaking out of hollow forms can be a skin-irritant. An additional and serious problem with unneutralized pickle is that when exposed to Liver of Sulfur patina, the pickle and the LOS combine to create a truly nasty gas, which, even in small quantities is extremely dangerous. So, neutralizing is essential.
The smaller side backplates are then completed by soldering the links/jumprings, bezels, flattened gold granules, and prongs.


Lots of clean-up to do, but very satisfied!!!! Oops, found one bezel that was not completely soldered down to the backplate, so back to the soldering bench, pickle and a little baking soda bath again.
After this I add some texture using the hammer handpiece again. This will show around the edges of the enameled units, once they are prong set.
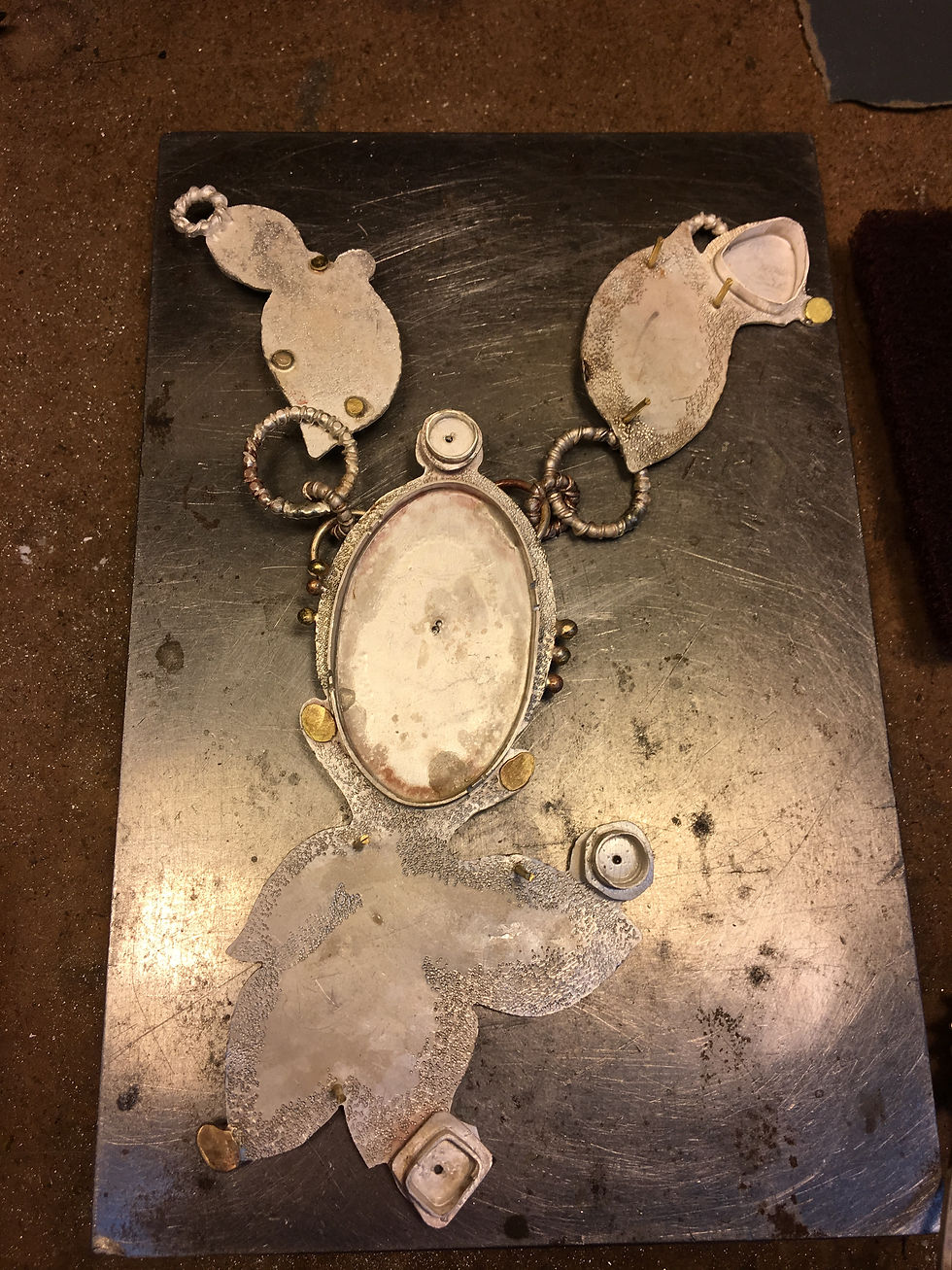
Getting to the Catch and Chain (Whew!)
I made a long length of Roman/Loop-in-Loop chain in Fine Silver and will use that for this neckpiece. If you want to know how to make one, buy a copy of “Classical Loop-in-Loop Chains” by Jean Stark <http://www.brynmorgen.com/CLLC.html>. It’s the best, and only, book on this subject.
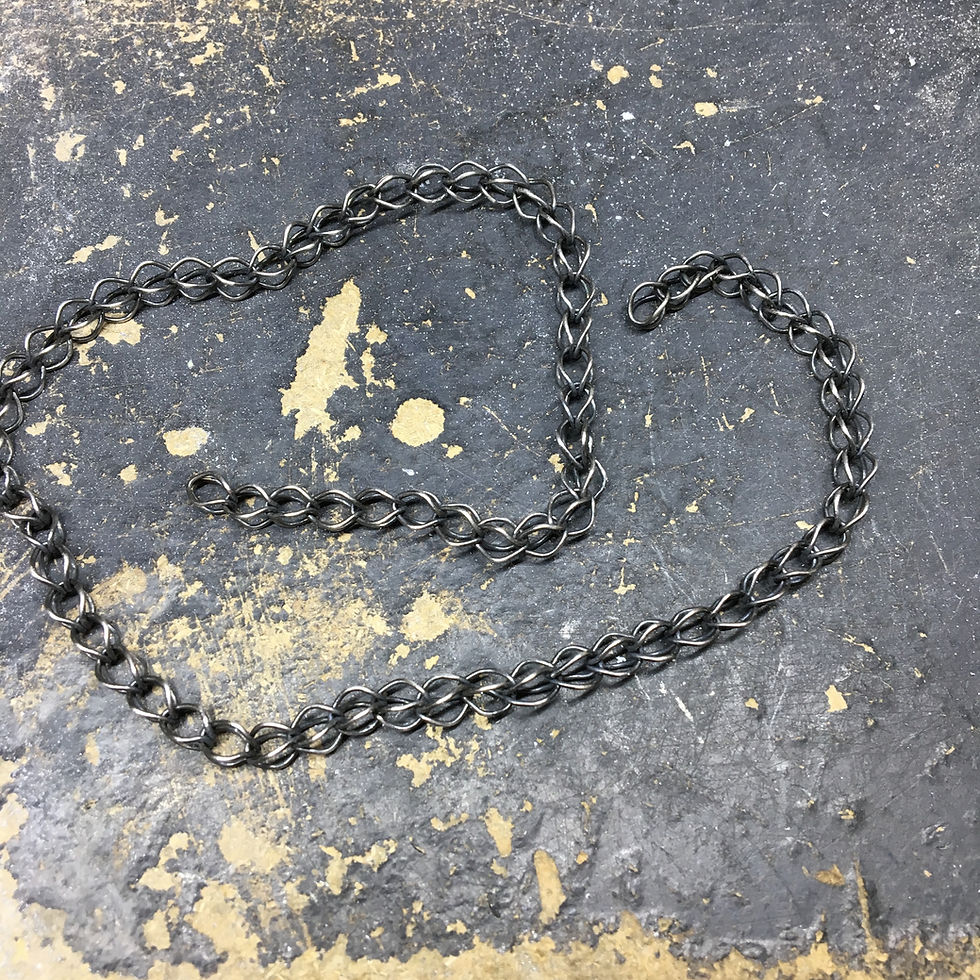
I always have a problem determining necklace lengths (something to do with being calculolexic, I guess). My process of doing this is to make all the parts, and then measure the length to see that the pendants sit where I want them on a human being (usually me, at least for measuring).
So, the clasp consists of two parts: the hook and the loop. The hook part has already been soldered and completed. The loop units needed to be assembled from their separate parts: two tapered cones; four sterling silver caps for the cones (two large and two small); four sterling silver, square wire bails (two small and two large).
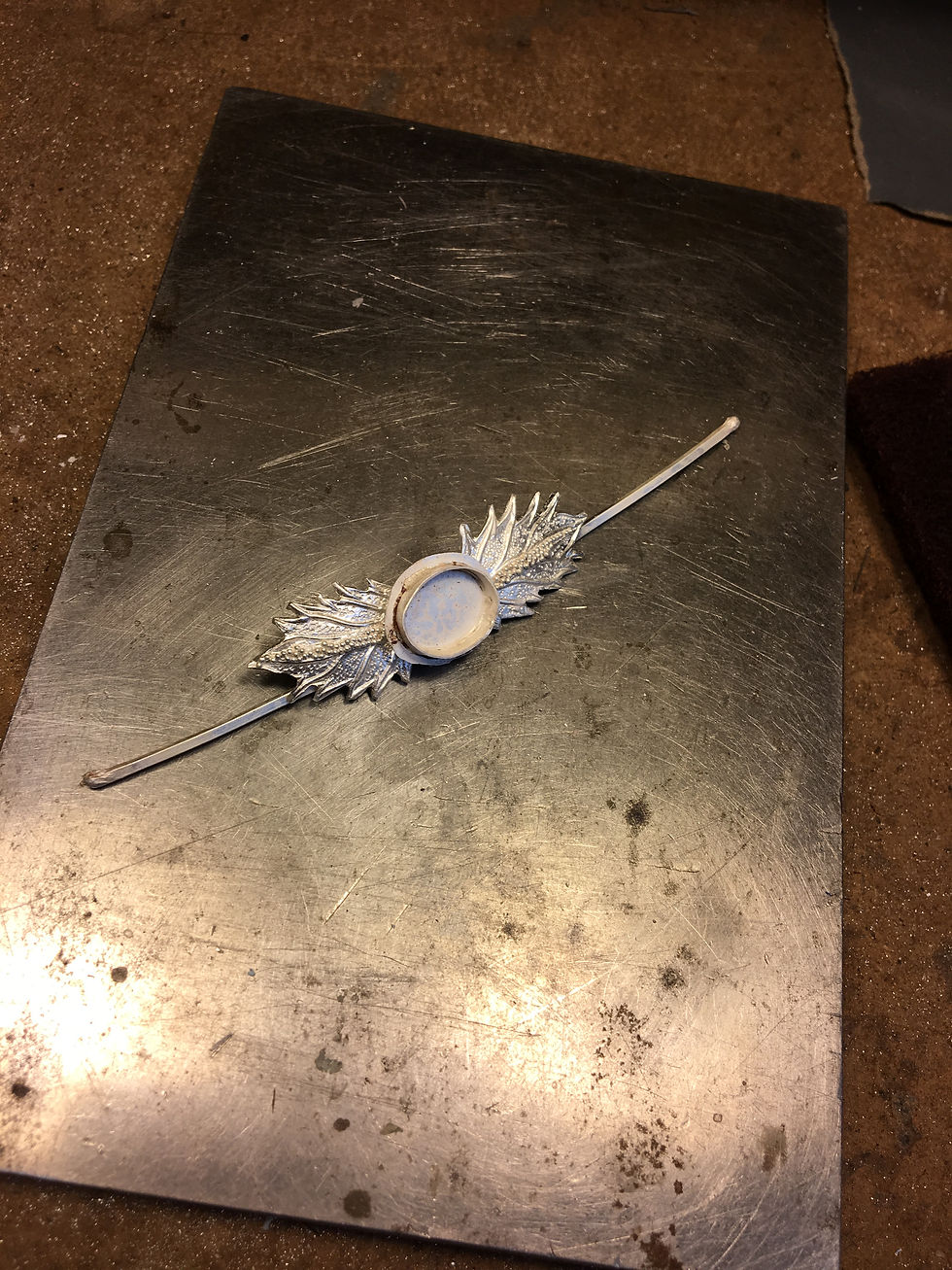

Finally able to throw the pieces in the magnetic finisher after cleaning up some of my messes. They come out nice and shiny, and any remaining flaws can now be attended to.
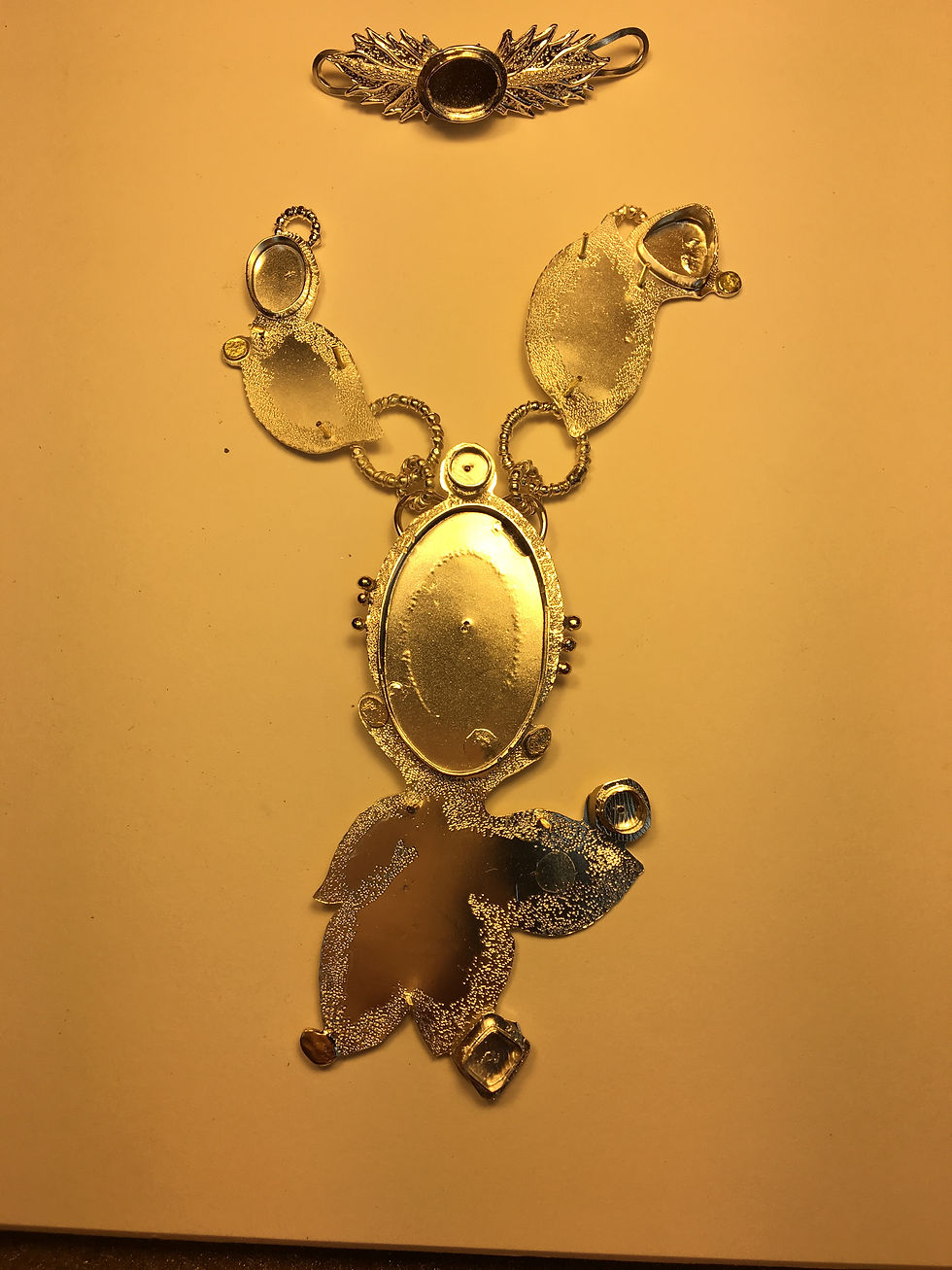
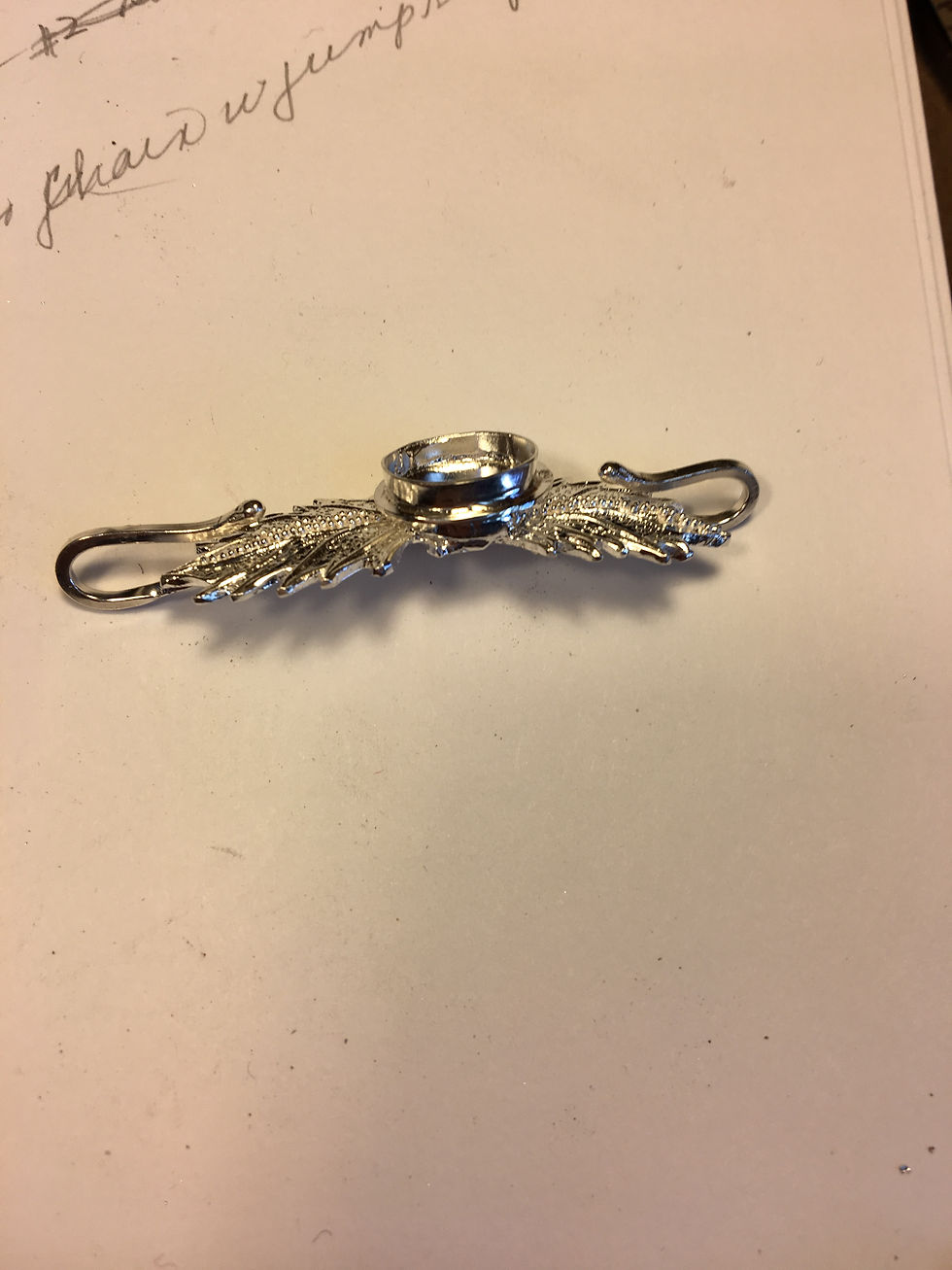
The loop units have to assembled carefully, because the chain has definite directionality. That is, there are four surfaces to each link (it’s really a sort of squared off chain. I need to determine how those squared loops will lay and join the bails to the tapered units, so that the chain does not twist once the bails are joined. This is also not an easy process for me, as the dyslexia, though mild, challenges my spatial relationship skills.
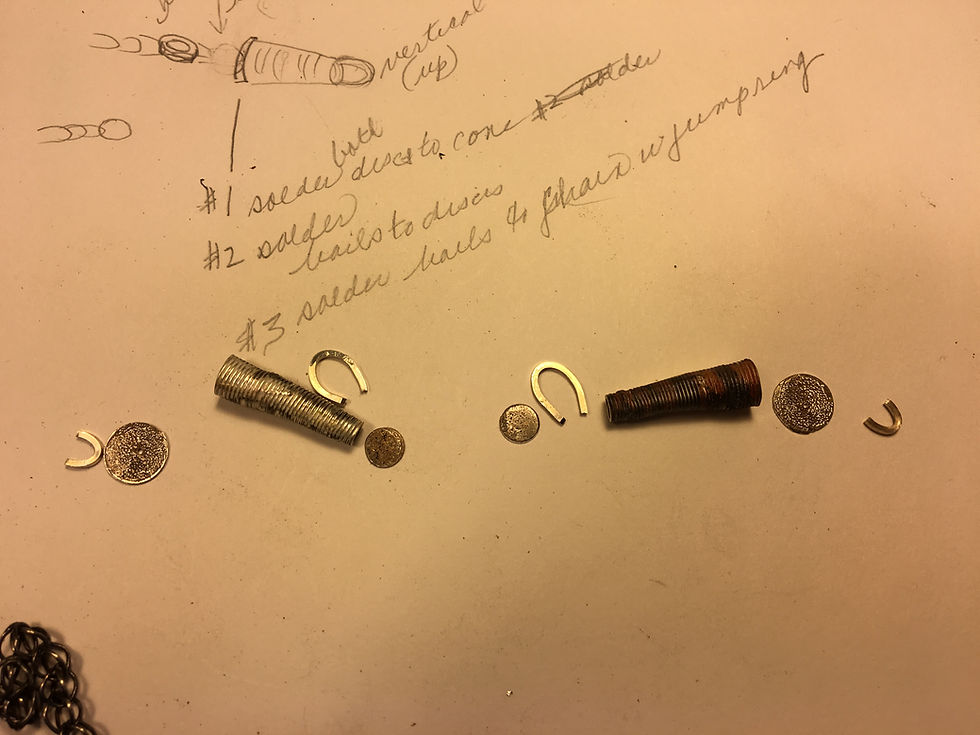
First, end caps are soldered to the wider end of each of the tapered units. Then, the small bails are soldered to those caps. Next the smaller end caps are soldered to the narrow end of the tapered units, and the longer bail is solder to those. If you think of the clasp as similar to a hook-and-eye, this has created the loop for the clasp.
Now the loop is soldered to the chain with a jump ring, pickled, and given it’s baking soda bath.
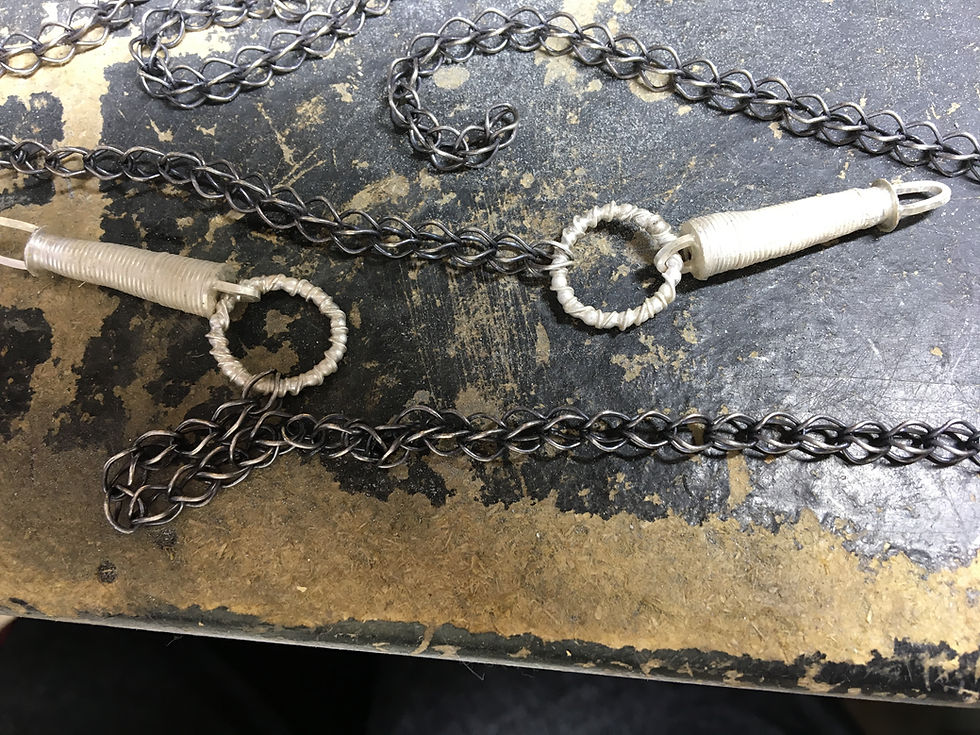
I want to tumble the chain and the loop units in the magnetic finisher. To accomplish this without tangling the chain, I coil the chain and use a short length of copper wire to hold the coil together.
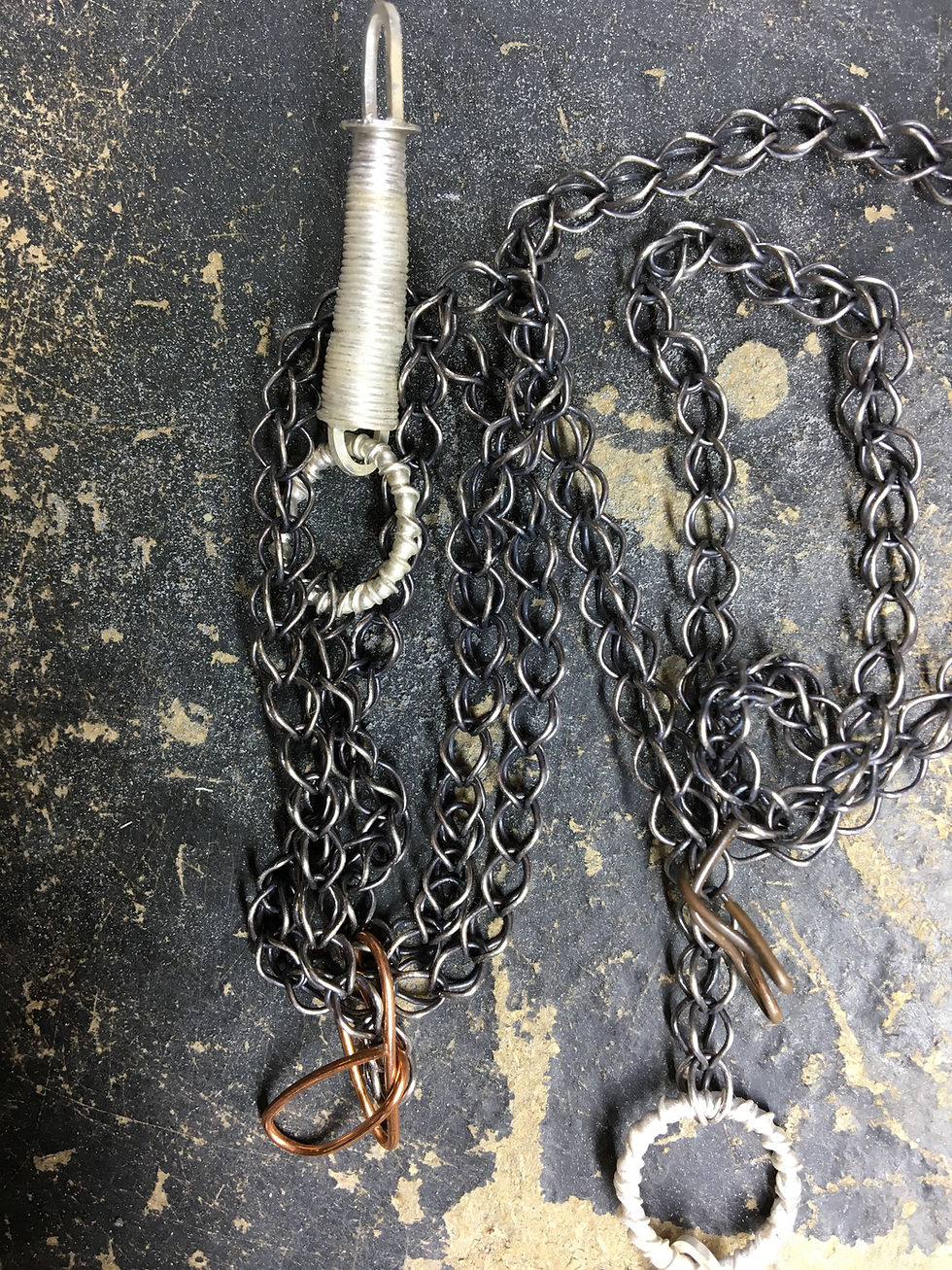
I wait to solder the final jump ring that would join the pendants (backplates) to the chain, because I want to determine the final length. The next step is to do that. I shouldn’t need to pickle after the soldering step because it’s such a small, specific joint, and any flux will just pop off the jump ring with a little pressure from flat nose pliers. So, no baking soda bath is needed.
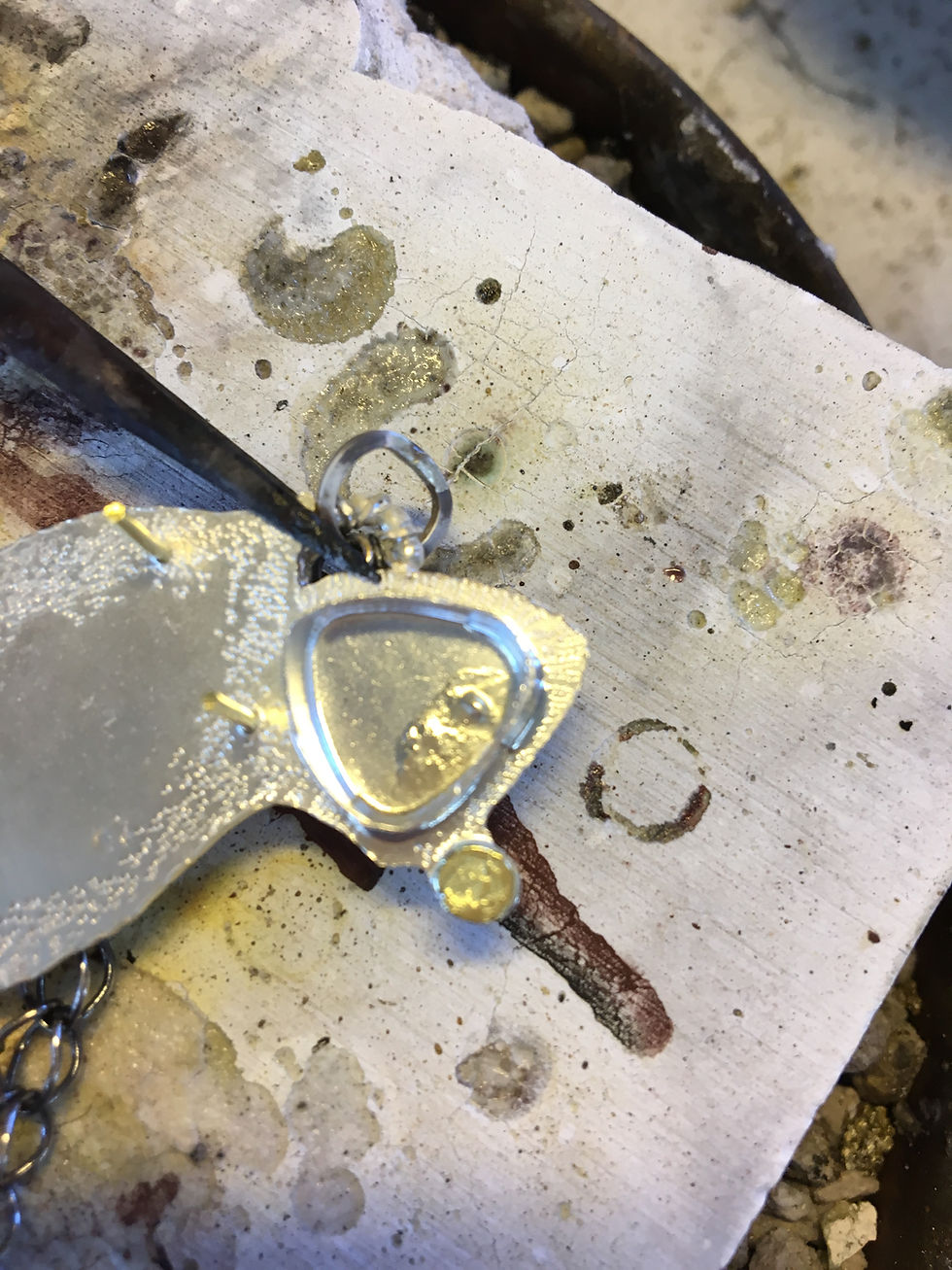
I also don’t need to put the piece in the finisher again, but can simply use Radial Bristle Discs and the flex shaft to finish the jump rings.

PATINATION
I want the entire piece to be patinated, except for the enameled units, as I want them to reflect light differently and more brightly than the rest of the piece. I patinate the entire piece in Liver of Sulfur. For instructions on how to do this, you can take a look at my book, “Pure Silver Metal Clay Beads” or check out Brynmorgen’s “Patina Basics”.

I then need to completely dry the neckpiece. The hollow units (the tapered forms of the clasp, the bezel settings on tubing, and the leaf unit) all sucked in water and Liver of Sulfur. I place the neckpiece in a toaster oven, set at 200 degrees F, for twenty minutes.
While the neckpiece is in the toaster oven, the enameled units are tumbled in the magnetic finisher.
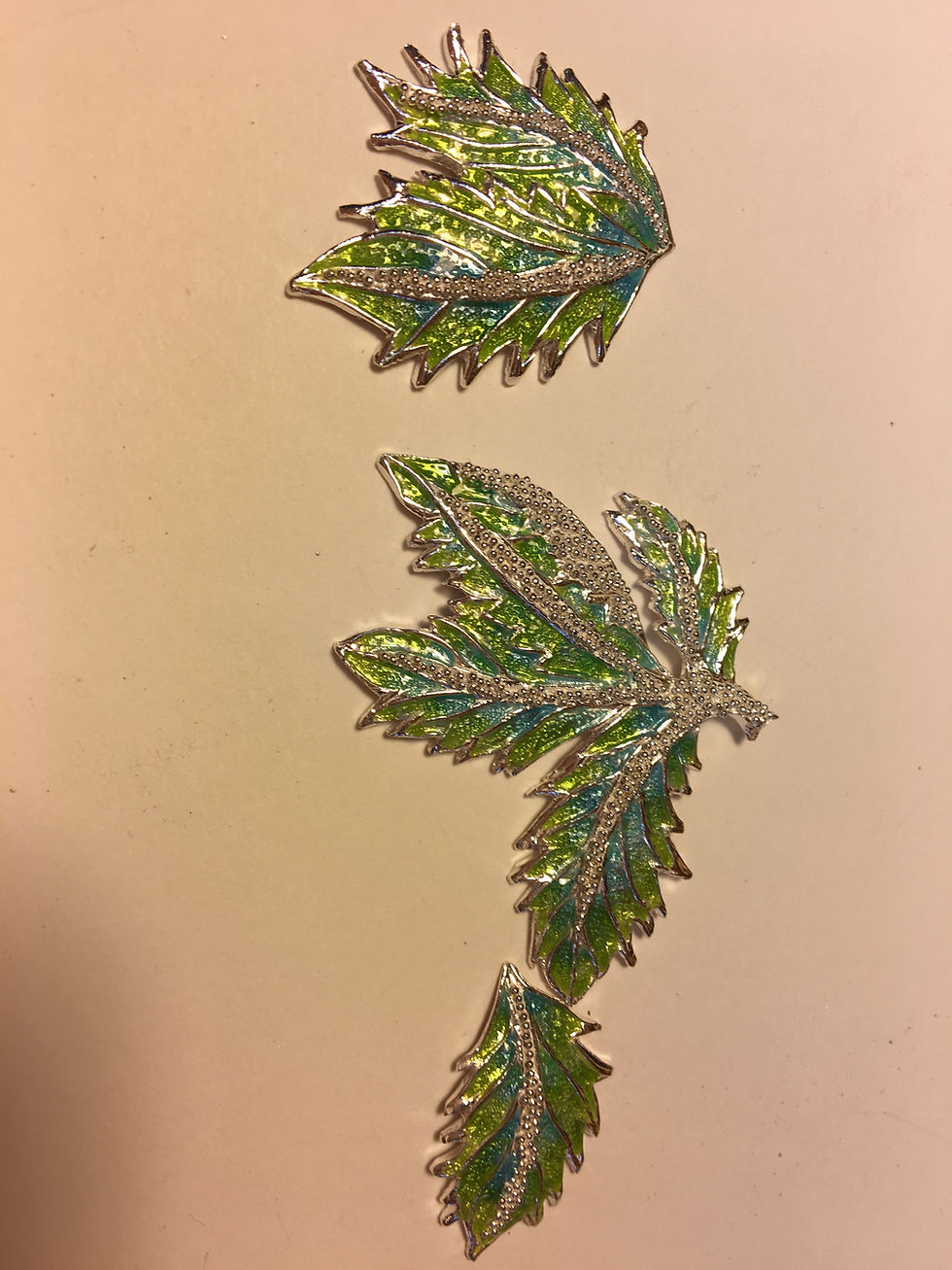
After drying, the neckpiece is brightened using the finest (pale green) Radial Bristle Discs in the flex shaft and a very light touch. I don’t want to remove the patina, I just want to brighten the metal.
SETTING THE STONES AND THE ENAMELED UNITS
I am quite nervous about setting the enameled units, since I am never quite certain that I have the prongs in the right locations to secure the units. I’m going to set these units before setting the stones, because, if the prongs are in the wrong place or insufficient to hold the units, then I would need to adjust them or create additional prongs. If I have to create additional prongs, I don’t want to have to remove any stones I might have set, in order to do the soldering that would be required. So, the stones will be set only when I know that the enameled units are secure.
However, I seem to have accurately placed the prongs and the enameled units are held quite securely.
After setting the enameled units, my next task is to set the stones. I begin by setting the smallest stones first: the two amethysts; the boulder opal; the lavender chalcedony, the carved aquamarine; and the green quartz (for the clasp). The final stone I set is the large dendritic agate.
A little secret: Under translucent stones I place a shim of highly polished Fine Silver sheet, to reflect a little light. I use Fine Silver because I know that it will not tarnish the way that Sterling Silver would. I use the shims because the interior of all the bezels is quite dark due to the patination. I could spend the time polishing the interior of the bezel settings, but I prefer to use the shims instead. I originally made the bezel walls a little high to accommodate the thickness of the fine silver shim.
You might have noticed that I set faceted stones upside down. I’ve never been a fan of faceted stones, but I like a little bit of sparkle. Setting them this way, gives me a that sparkle and also a contrast with the smoothness of cabochons.
Final Image of the Completed Neckpiece will be posted this week. Keep Checking!
The Tools and Materials I used for this neckpiece
Sketchbook
Pencil
Prismacolor pencils
Dendritic agate.
Amethyst
Aquamarine
Lavender Chalcedony
Quartz
Boulder Opal
Sterling Silver (sheet, square wire, round wire, beaded wire, round tubing)
Fine Silver (from metal clay)
Fine Silver (granules, bezel sheet, round wire)
18k Gold (wire, sheet)
Oval and round templates
silicone block printing plates
lino carving tool
olive oil release (for metal clay)
PVC Roller
Thickness gauge (playing cards)
Metal clay non-stick surface
Photocopier with toner
PMC3
PMC3 Slip
small-tipped Shapers
sanding boards
artist knife
needle tool
Computer-controlled kiln
kiln pad
alumina hydrate
220 grit emery paper
Flexible shaft machine
hammer handpiece for flex shaft
Transparent, lead-bearing, vitreous enamels
fine watercolor brush
porcelain enamels tray
KlyrFire
distilled water
eye dropper
Enamel firing tools (trivets, nichrome wire, grids, fork, tweezers)
enameling kiln
heavy grit sandpaper
rolling mill
rubber abrasive wheel
scribe in a pin vise
jeweler’s saw frame and 6/0 saw blades
steel dividers
masking tape
flush cutters
scissors
mill bastard file
mitre jig
Hard, Medium, Easy silver solder
Acetylene/Air torch
ventilation
carborundum in steel bowl
miniature drill press
#60 drill bit
Steel stamps/ punches (sterling silver, fine silver, 18k gold and hallmark)
Chasing hammer
tapered steel mandrel and winding tool (to make the tapered forms)
drawplate
planishing hammer
paste flux
titanium solder picks
soldering tweezers
fireproof surface
soldering blocks
yellow ochre powder
pickle (Sparex)
pickle pot
copper tongs
baking soda
hotplate
stainless steel pot
water
magnetic finisher and burnishing liquid
Liver of Sulfur chunks
toaster oven
Radial Bristle Discs (3M)
bezel pusher
prong pusher
January 17, 2017
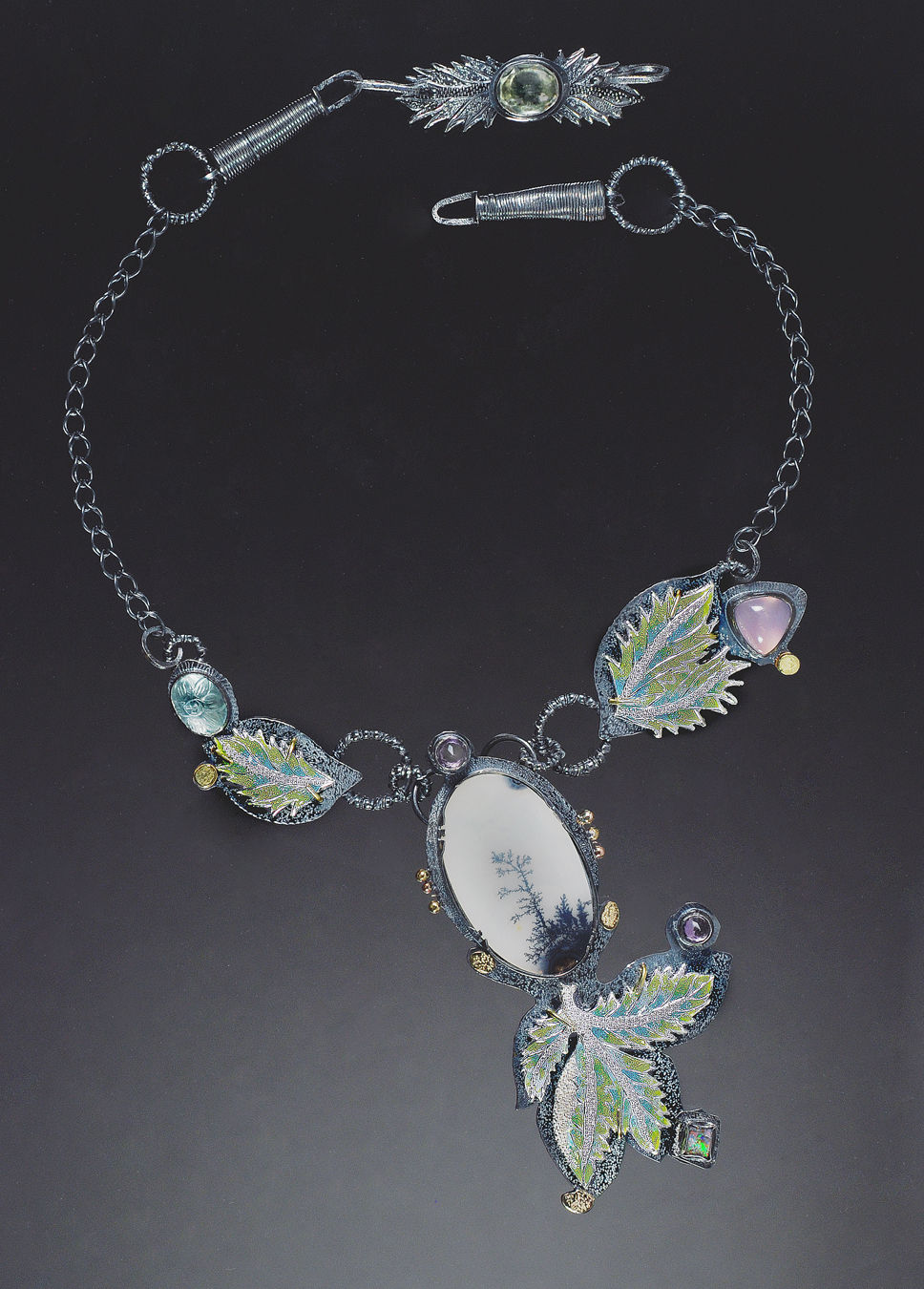
Title: You Tried to Bury Us; You Forgot We Were Seeds
Form: Neckpiece
Materials: Fine and Sterling Silver, 18k Gold, dendritic agate, boulder opal, amethyst, lavender chalcedony, aquamarine, vitreous enamels
Jewelry Fabrication Techniques: soldering, sawing, patination, metal clay, stone setting, enameling, handmade chain
Dimensions: 4” high x 2” wide 1/8” deep(101.6mm high x 50.8mm wide 3.175mm deep)
Year: 2017
Photography: Evan J. Soldinger
Recent Posts
See AllMagnetic Finishers And Their Variables I always use a magnetic finisher to burnish my pieces right out of the kiln, whether I’m planning...
I have always felt that when I sit down at the bench, there would never be a time when I did not know what I would be making. I would...